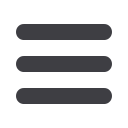

3D printed horseshoes
Researchers at the Commonwealth Scientific
and Industrial Research Organization (CSIRO),
Australia, used 3D modeling software to design a
lightweight racing shoe with a perfect fit for a race-
horse nicknamed “Titanium Prints.” Traditionally
made from aluminum, horseshoes can weigh up to
1 kg, but horse trainer John Moloney says that the
ultimate race shoe should be as lightweight as pos-
sible. “These titanium shoes could take up to half
of the weight off a traditional aluminum shoe,
which means a horse could travel at new speeds,”
explains Moloney. The precision scanning process takes just a few minutes and shoes can be made to measure
for each hoof and printed the same day.
CSIRO’s titanium expert, John Barnes, says that 3D printing a race horseshoe from titanium is a first for sci-
entists and demonstrates the range of applications the technology can be used for. “There are so many ways we
can use 3D titanium printing. We are helping companies create new applications like biomedical implants and
even things like automotive and aerospace parts. The possibilities really are endless with this technology,” says
Barnes.
www.csiro.au.
Micro-windmills to recharge cell phones
A University of Texas-Arlington research associate and electrical engi-
neering professor designed a micro-windmill that generates wind energy
and may become an innovative solution for cell phone batteries constantly
in need of recharging. The device is roughly 1.8 mm at its widest point—so
hundreds of them could be embedded in a sleeve for a cell phone. Wind,
created by waving the cell phone in air or holding it near an open window
on a windy day, would generate the electricity that could be collected by the
cell phone’s battery. Smitha Rao designed the windmills and blended
origami concepts into conventional wafer-scale semiconductor device lay-
outs. The result is that complex 3D moveable mechanical structures can
self-assemble from 2D metal pieces using planar multilayer electroplating
techniques optimized by WinMEMS Technologies Co., a Taiwanese fabri-
cation foundry.
www.uta.edu.
Insulating firebricks
Morgan Advanced Materials, Windsor, England, recently introduced a
full product range of insulating firebricks (IFBs). Manufactured by its Ther-
mal Ceramics business, 10 different grades are available to meet the temper-
ature needs of multiple applications, from 2300°-3300°F. The K-23 IFB is
manufactured with a unique slurry casting process that produces low ther-
mal conductivity and good thermal shock characteristics. Rated at 2300°F,
the brick has low density, high hot strengths, good thermal stability, and
ultra-low thermal conductivity. It experiences much less shrinkage than
competitive products, significantly improving its lifetime. A variety of other
low temperature options are available that offer tile brick in a large shape
format with low shrinkage and insulation stability. For high temperature
kiln linings, Insalcor is a high temperature firebrick with a use limit to
3250°F. The bubble alumina brick is produced by a manufacturing process
that features excellent strength and thermal stability at high temperatures
and great thermal shock resistance for high temperature cycling furnaces.
www.morganadvancedmaterials.com.
ADVANCED MATERIALS & PROCESSES •
MARCH 2014
5
interest
of material
A micro-windmill is pictured on the face of a
penny. Courtesy of UT Arlington.
3D printed titanium horseshoes.
K-23 insulated firebricks are suitable for the
ceramics market, including kilns, furnace linings,
and cyclical furnaces.