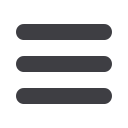
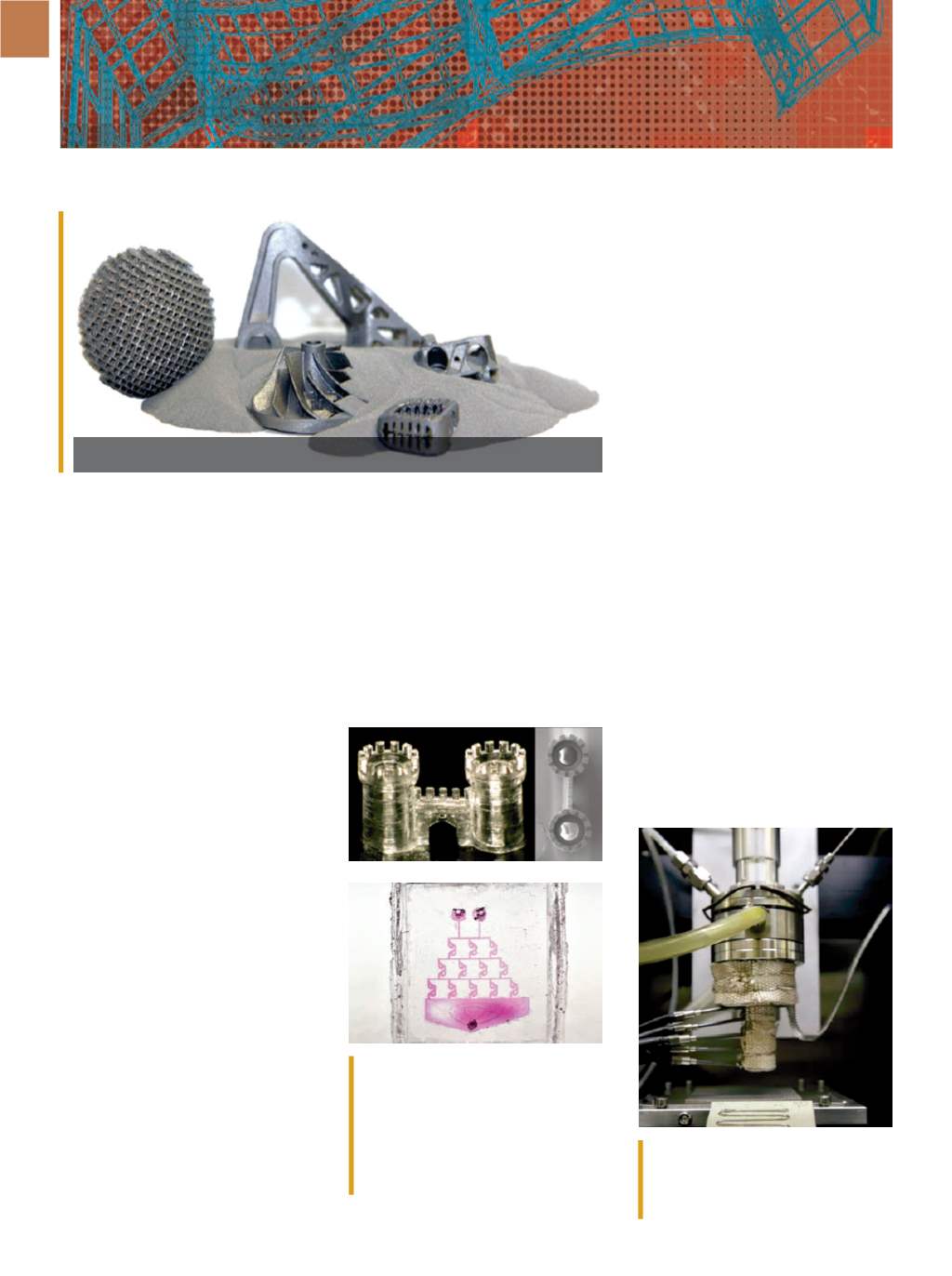
8 0
A D V A N C E D M A T E R I A L S & P R O C E S S E S | M A Y / J U N E 2 0 1 7
3D PRINTSHOP
ROLLING BACK PRICES ON
TITANIUM POWDER
Researchers at the University of
Utah, Salt Lake City, are working on a
potentially disruptive manufacturing
technology that could dramatically
reduce the cost of titanium (Ti) pow-
ders. Additive manufacturing requires
low-oxygen content powders, which
in the case of Ti, has proven difficult
and expensive to make. Utah research-
ers, in cooperation with Boeing and
Arconic Inc., developed a way to turn
low-cost commercial TiO
2
into low-ox-
ygen Ti powder, and they are begin-
ning to scale up and validate the pro-
cess for industrial applications. The
work, led by Professor Z. Zak Fang, is
jointly funded by the Advanced Re-
search Projects Agency-Energy (AR-
PA-E) and Utah’s two industry partners.
http://powder.metallurgy.utah.edu.
KIT RESEARCHERS DEMO
GLASS PRINTING PROCESS
Nearly four years ago, as interest
in 3D printing peaked, Karlsruhe In-
stitute of Technology (KIT), Germany,
began working on a process that at the
time may have seemed out of step. In-
stead of studying an advanced alloy
or engineered polymer, KIT scientists
set their sights on printing with glass
and they are now disseminating the
results of their work. The key to the
A 3D printer developed by LLNL and WPI
employs a direct metal writing process
that uses semisolid liquidmetal instead
of powders.
glass printing process is a photosensi-
tive slurry made by mixing nanoparti-
cles of high-purity quartz with a small
amount of liquid polymer. The mixture
is cured by means of stereolithography,
followed by removal of any remaining
liquid including the polymer. As a final
step, the structure is solidified by sin-
tering, causing the glass particles to
fuse. To see a video of the process, visit
http://bit.ly/2pG7WZJ.METAL 3D PRINTING
REINVENTED
Printed metal parts are often
plagued by gaps, cracks, and other
defects, making validation a slow and
expensive process. Most efforts to ad-
dress the problem focus on improving
powders, but Lawrence Livermore Na-
tional Laboratory (LLNL) and Worches-
ter Polytechnic Institute (WPI) are tak-
ing a different approach with
direct
metal writing,
a process that extrudes
metal directly onto the part. Instead of
using powder as the starting material,
researchers use an ingot that is main-
tained in a semisolid state so it behaves
like a solid at rest, but flows like a liquid
under an applied force as when extrud-
ed through a nozzle. The resulting met-
al beads harden uniformly as they cool,
minimizing the presence of oxide and
residual stress in the final part. Having
proven the concept using bismuth-tin,
the collaborators are now moving on to
aluminum alloys. Aluminum has great-
er application potential, but its higher
melting point will complicate its use. To
see a video of the direct metal writing
process, visit
http://bit.ly/2p9nHrf.
Complex glass structures produced at
KIT demonstrate the capabilities of a 3D
printing process that uses stereolitho-
graphic techniques. Structures just a few
centimeters in size with features on the
order of a fewmicrons can take almost
any imaginable form.
Low-cost Ti-6Al-4V spherical powder produced at the University of Utah.