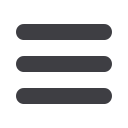
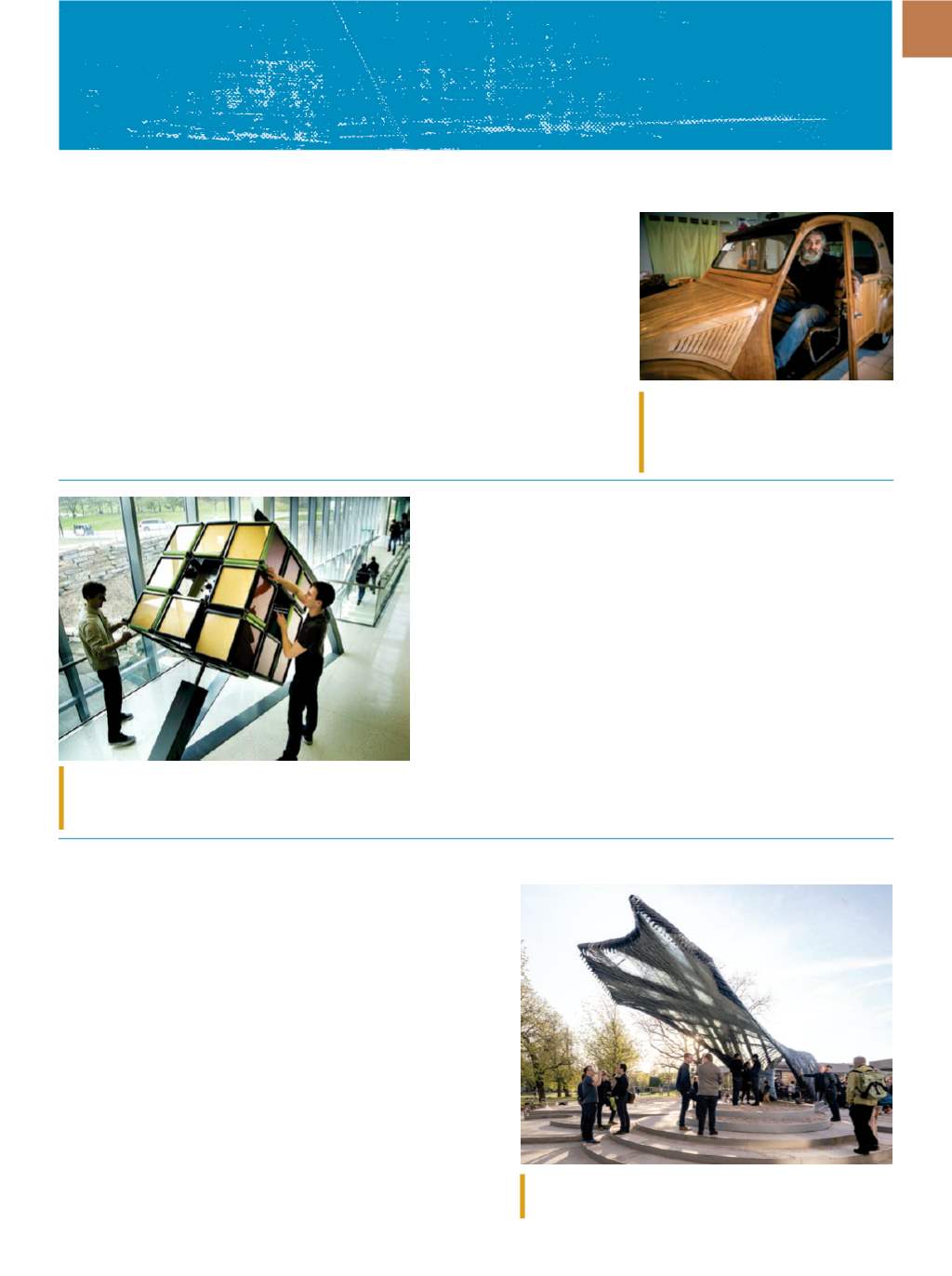
A D V A N C E D
M A T E R I A L S
&
P R O C E S S E S |
M A Y / J U N E
2 0 1 7
7 9
STRESS RELIEF
WOOD YOU LIKE TO DRIVE?
French cabinetmaker Michel Robillard handcrafted a wooden replica of Citroen’s
1948 2CV automobile using a combination of apple, pear, and cherry lumber. The fully
functional vehicle took six years to build, including an undulating hood carved out of a
single block and featuring 22 ridges honed with a wood chisel and sandpaper. The 2CV,
which stands for “deux chevaux” (two horsepower), was launched as Citroen’s competi-
tion against the Volkswagen Beetle. The vehicle is equipped with an original engine from
Citroen’s 3CV model, giving it the extra boost required to propel the heavier wooden
structure. Besides the engine, the car’s metal frame, wheels, and headlights are the only
parts the Frenchman did not make himself. The car is not for sale: Robillard hopes to put
it on display in an art gallery or see it featured in a big-budget advertisement or movie.
afp.com.
DRONES WEAVE MOTH-INSPIRED PAVILION
Researchers and students from the University of Stuttgart, Ger-
many, employed robots and drones to weave a novel 39-ft composite
pavilion inspired by moth webs. The pavilion is based at the school’s
Institute for Computational Design and Construction, and Institute of
Building Structures and Structural Design. It is a singular cantilever
structure created by laying 114 miles of glass and carbon fiber-rein-
forced composites. The design mimics silk hammocks spun by two
species of moth larvae
(Lyonetia clerkella
and
Leucoptera erythrinella)
and the structure was manufactured offsite through a process the re-
searchers call “multi-machine cyber-physical fabrication.” During con-
struction, two stationary industrial robotic arms are placed at the ex-
tremities of the structure, while a drone passes fiber from one side to
the other. In addition, an adaptive control and communication system
allows the robot and drone to interact throughout the winding and fi-
ber laying processes. The team believes this prototype process could
be developed to construct other composite structures in the future.
www.itke.uni-stuttgart.de.
PUZZLE ME THIS
A giant Rubik’s Cube newly installed on the University of Michigan’s
North Campus is believed to be the world’s largest hand-solvable, station-
ary version of the famous puzzle. The 1500-lb, mostly aluminum structure
was unveiled in April on the second floor of the G.G. Brown engineering
building. It was imagined, designed, and built by two teams of mechan-
ical engineering undergraduate students over the course of three years.
The colorful cube is meant to be touched and solved, and the students
worked hard to figure out a movement mechanism to enable that. They
realized they could not simply scale up the design of the handheld cube
because the friction would be too great. To keep friction to a minimum,
they devised a setup that utilizes rollers and transfer bearings. The team
considers the finished cube a fusion of art and engineering.
umich.edu.
Jason Hoving and Ryan Kuhn place a giant Rubik’s Cube
into the lobby of the G.G. Brown engineering building.
Courtesy of University of Michigan.
Robillard spent six years cra ing this fully
functional, life-size 2CV Citroen out of
apple, pear, and cherry wood.
Courtesy of afp.com.
Composite pavilion inspired by moth webs.
Courtesy of Ghinitoiu.