
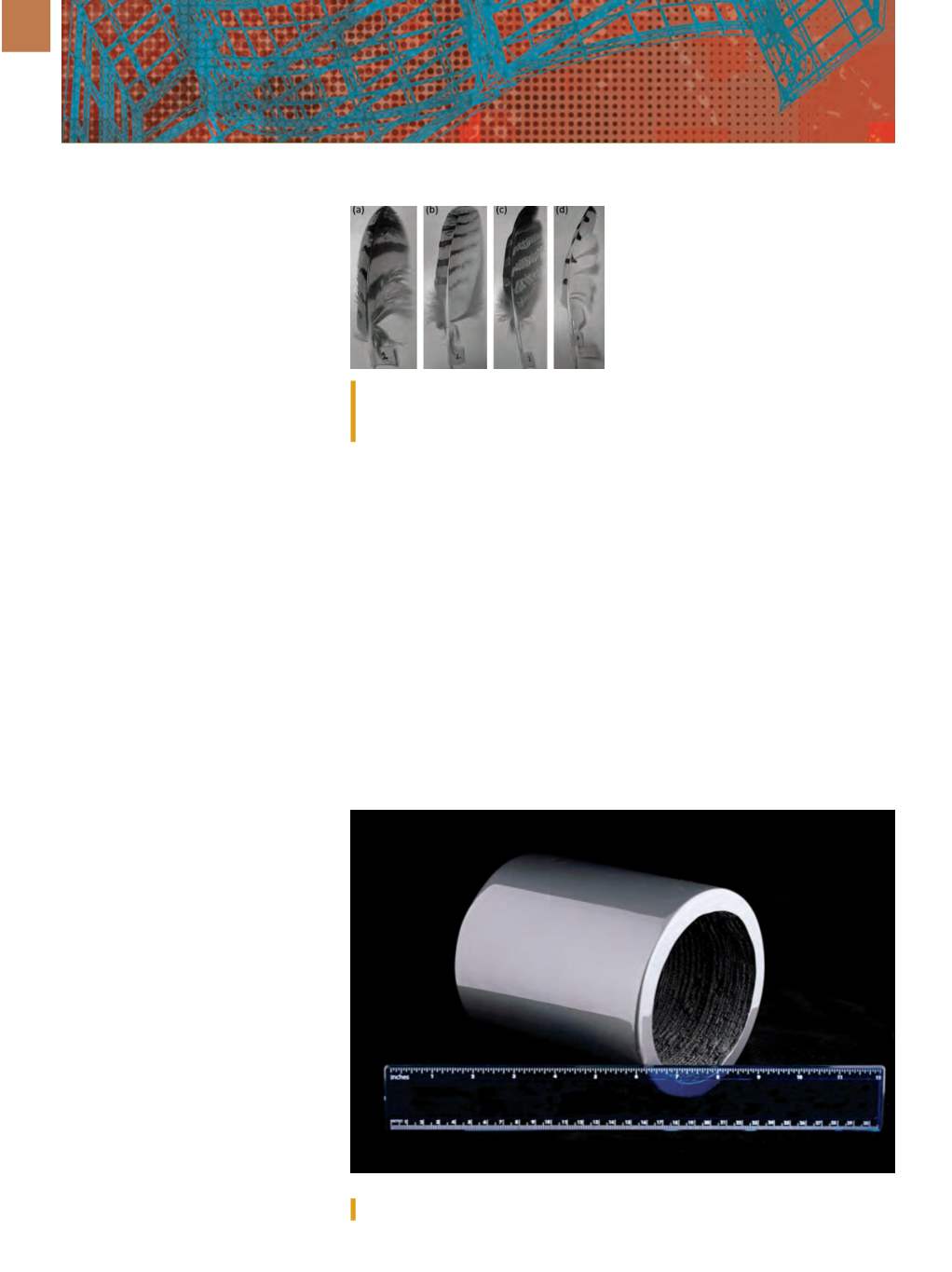
A D V A N C E D M A T E R I A L S & P R O C E S S E S | J A N U A R Y 2 0 1 7
5 2
3D PRINTSHOP
THE SOUNDOF SILENCE
Inspired by feathers that suppress
flight sound, researchers developed a
3D-printed plastic attachment that can
be retrofitted to an existing airfoil design
to reduce wind turbine noise. The sci-
entists—from Lehigh University, Virginia
Tech, Florida Atlantic University, and the
University of Cambridge—modeled their
device on down from owl wings. The
down consists of hairs that rise almost
perpendicular to the feather surface,
then bend in the flow direction to form
a canopy at the top like a microscopic
forest. The canopy pushes off the noisy
air flow, suppressing frequencies over
1.6 kHz—including the range of greatest
sensitivity in human hearing. To mimic
this structure, the device consists of
small “finlets,” which can reduce turbine
noise by 10 dB without affecting aerody-
namics. This kind of noise reduction has
implications beyond wind turbines and
aircraft, and could be applied to other
aerodynamic situations such as wind
noise in automobiles.
lehigh.edu, vt.edu,
fau.edu,
www.cam.ac.uk.
GE INITIATIVE ADDS ON
GE, Fairfield, Conn., will purchase
controlling shares of Arcam AB, Swe-
den, inventor of electron beam melting
machines for metal-based additive man-
ufacturing and a producer of metal pow-
ders for the aerospace and orthopedic
industries. Arcam also operates AP&C,
Canada, a metal powders operation, and
DiSanto Technology, Shelton, Conn., a
medical additivemanufacturing (AM) firm,
in addition to sales and application sites
worldwide. The purchase comes on the
heels of GE’s $599 million acquisition of a
75% stake in Concept Laser GmbH, Ger-
many, which designs and manufactures
powder bed-base laser AM machines for
the aerospace, medical, and automotive
industries, among others. Concept Laser
processes powdermaterials including tita-
nium, nickel-base, and cobalt-chromium
alloys, as well as hot-work and high-grade
steels and aluminum. The recent acqui-
sitions dovetail with GE’s ongoing AM
efforts, which include a $1.5 billion invest-
ment in manufacturing and additive tech-
nologies at their Global Research Center
and the development of a worldwide net-
work of centers for advancing AM science.
geadditive.com.
PRINTING PREVAILS IN
MAGNET MANUFACTURE
Scientists at the DOE’s Oak Ridge
National Laboratory (ORNL), Tenn.,
demonstrated that additive manufac-
turing (AM) can produce permanent
magnets with mechanical, microstruc-
tural, and magnetic properties superior
to those of bonded magnets made
using traditional methods—all while
conserving critical materials. To fabri-
cate the isotropic, near-net-shape, neo-
dymium-iron-boron bonded magnets,
the Oak Ridge team began with com-
posite pellets made of 65 vol% isotro-
pic NdFeB powder and 35% polyamide
(Nylon-12), then melted, compounded,
and extruded them using the Big Area
Additive Manufacturing machine. While
conventional sintered magnet manu-
facturing can result in material waste of
30-50%, AM reuses that material, pro-
ducing nearly zero waste, an especially
important factor when manufacturing
magnets with neodymium and dyspro-
sium—rare earth elements mined and
separated outside the U.S. AM is also
more efficient than traditional injection
methods. “Manufacturing is changing
rapidly, and a customer may need 50 dif-
ferent designs for themagnets they want
to use,” explains researcher Ling Li. AM
allows eachmagnet to be crafted quickly
using computer-assisted design instead
of requiring individual mold making and
tooling
. ornl.gov.Feathers from (a, b) Eurasian eagle owl,
(c) great gray owl, and (d) snowy owl.
Courtesy of Ian A. Clark, et al.
This isotropic, NdFeB bonded permanent magnet was 3D-printed at ORNL.