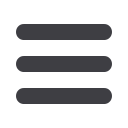
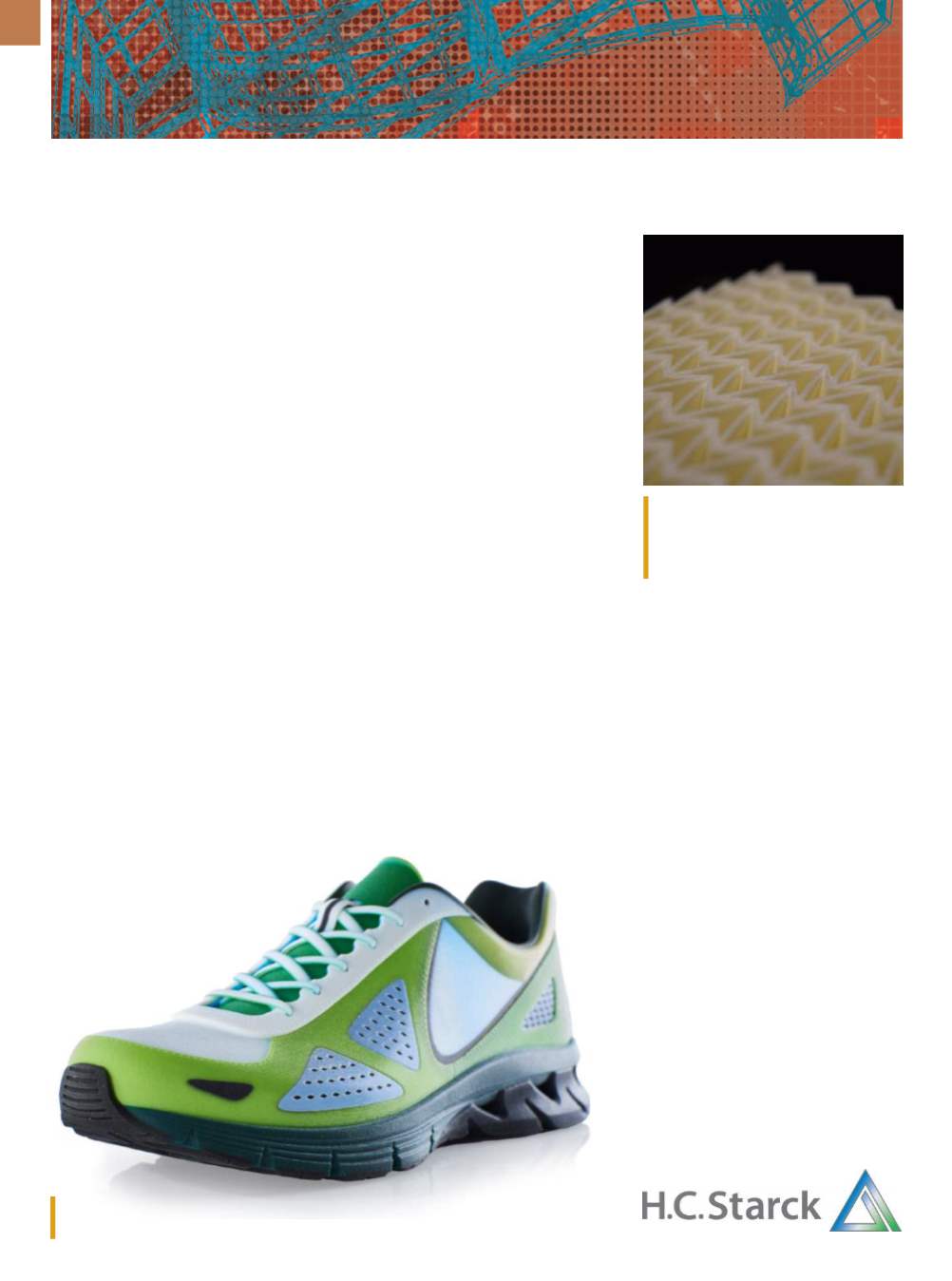
6 0
A D V A N C E D M A T E R I A L S & P R O C E S S E S | J U L Y / A U G U S T 2 0 1 6
3D PRINTSHOP
ONE-STOP PRINTER BUILDS COMPLETE ATHLETICSHOE
Prototype produced with full color, smooth surfaces, and a rubberlike sole, all in a single print
operation. Courtesy of Business Wire and Stratasys Ltd.
S
tratasys Ltd., Minneapolis, intro-
duced the J750 3D printer that
produces finished models with
colors, textures, andmultiple materials,
eliminating the need for post-process-
ing. For example, the J750 can print a
complete athletic shoe with full color,
smooth surfaces, and a rubberlike sole
in a single operation. Built-in PolyJet
Studio software is newly designed and
allows users to mix and match more
than 360,000 different colors plus mul-
tiple materials and material proper-
ties—from rigid to flexible and opaque
to transparent. Color textures can be
loaded intact via VRML files imported
from CAD tools.
The machine also offers increased
efficiency over previous models. Its
six-material capacity keeps the most
used resins loaded and ready for print-
ing, while newly designed print heads
allow simulated production plastics
such as Digital ABS to be printed in half
the time of other Stratasys PolyJet sys-
tems. Finally, the J750 is expected to
improve total cost of ownership. Design-
ers and engineers can handle product
prototypes within hours of developing
an initial concept and receive immediate
feedback, eliminating processes, time,
and resources typically required to cre-
ate product-matching prototypes.
stratasys.com.
NOVEL MATERIAL BOOSTS
BRAIN PROTECTION
Helmet manufacturer Charles
Owen Inc., Lincolnton, Ga., was
awarded $250,000 to develop a new,
energy absorbing material that could
protect athletes and military person-
nel, among others, from brain injury.
The prize will support a collaboration
between the company, which produces
equestrian, motorcycle, and military
helmets, and Cardiff University, UK, cre-
ator of the multilayered, elastic mate-
rial called C3. The project will further
develop the material, which can be
precisely designed using mathemati-
cal modeling, and then computer test
it for specific impact scenarios prior to
fabrication with a 3D printer. During C3
production, a polymer-based powder
is fused into a specific shape by a laser,
which solidifies the material to form a
strong, flexible structure.
Funding was awarded by a part-
nership of the National Football League,
Under Armour, GE, and the National
Institute of Standards and Technology
as part of
Head Health Challenge III:
Advanced Materials for Impact Mitiga-
tion.
The team is among four winners
to secure initial funding; after a year,
the most promising technology will
receive another $500,000 to support
further development.
charlesowen.com,
www.cardiff.ac.uk.
POWDER PROCESS POWERS
UP FOR AM
H.C. Starck, Germany, launched
a new process to produce specialized
refractory metal powders for additive
manufacturing (AM). The company
will apply the new process to its exist-
ing products—molybdenum, tanta-
lum, niobium, and tungsten in pure
and alloyed powder forms—offering
spheroidized refractory metal powders
with tailored chemistry and particle
size distribution. The new powders are
engineered for enhanced processability
and performance when used with stan-
dard AM techniques such as binder jet,
directed energy deposition, and pow-
der bed fusion.
hcstarck.com.
C3 material can be designed using
mathematical modeling and tailored for
specific impact scenarios. Courtesy of
Cardiff University.