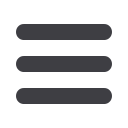
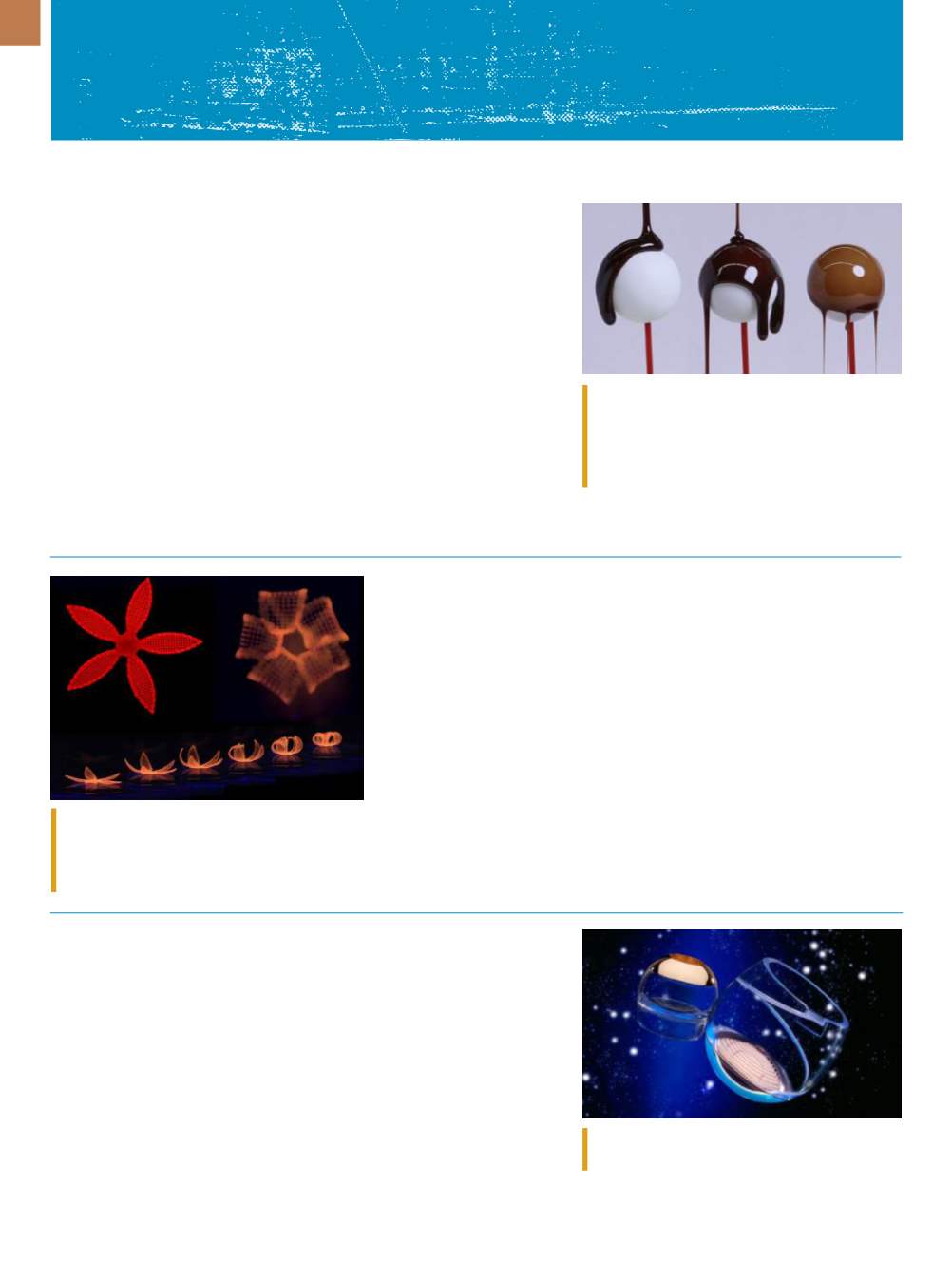
5 8
STRESS RELIEF
BONBONS PREDICT THINSHELL THICKNESS
A simple fabrication technique derived by engineers at Massachusetts
Institute of Technology, Cambridge, may help chocolate artisans create uni-
formly smooth shells and precisely tailor their thickness. The research could
also have uses far beyond the chocolate shop. By knowing just a few key vari-
ables, engineers could predict the mechanical response of many other types of
shells, from small pharmaceutical capsules to large airplane and rocket bodies.
The fabrication technique quickly creates thin, rubbery shells, in which
a liquid polymer is drizzled over dome-shaped molds and spheres such as
ping pong balls. Each mold was coated with liquid and cured over 15 minutes.
The resulting shell was peeled off the mold and was smooth—virtually free of
noticeable defects—with nearly uniform thickness throughout. Combining this
simple technique with the theory they derived, the team created shells of var-
ious thicknesses by changing certain variables, such as mold size and polymer
density.
web.mit.edu.
SHOWME THEWAY TO THE NEXTWHISKEY BAR
Ogle, UK, created awhiskey glassmodel able towithstand rigorous testing
that proves its suitability for use beyond earth’s atmosphere. The company’s
stereolithography (SLA) machines were used to create the precise specifica-
tions needed for the microgravity-friendly object. To ensure the prototype is
visually realistic and durable, a resin called ClearVue was selected for produc-
tion due to its moisture resistance.
The model was eventually hand-finished inside and out using 800 wet
grade paper to remove any layering and provide a smooth texture. To create
a glasslike appearance, it was masked and clear lacquered on both sides.
The glass, made of six component parts, was subject to many pre- and post-
production checks by the team. This included applying a rose gold-plated
base to ensure that the thread, which brings liquid to the top of the glass and prevents spills, fits correctly and with enough clear-
ance for the paint team. The prototype was tested in microgravity at the ZARM Drop Tower in Germany where it was approved for
space flight.
oglemodels.com.
4D-PRINTEDHYDROGELS TRANSFORMUNDERWATER
A team of scientists at Harvard University, Cambridge, Mass., unveiled
4D-printed hydrogel composite structures that change shape upon immersion
in water. The team was inspired by natural structures such as certain plants
that change their form over time according to environmental stimuli. The new
hydrogel composites are programmed to perform precise, localized swelling
behaviors. The composites contain cellulose fibrils that are derived from wood
and are similar to the microstructures that enable shape changes in plants.
By aligning cellulose fibrils during printing, the hydrogel composite ink is
encoded with anisotropic swelling and stiffness that can be patterned to pro-
duce intricate shape changes. The anisotropic nature of the cellulose fibrils
gives rise to various directional properties that can be predicted and controlled.
The new method opens up many potential applications for 4D-printing tech-
nology including smart textiles, soft electronics, biomedical devices, and tissue
engineering.
wyss.harvard.edu.
A series of images shows the transformation of
a 4D-printed hydrogel composite structure after
being submerged in water. Courtesy of Wyss
Institute at Harvard University.
Inspired by videos of chocolatiers making bonbons
and other chocolate shells, Pedro Reis and his team
wondered if there is a way to precisely predict the
final thickness of chocolate and other shells that
start as a liquid film.
This 3D-printed whiskey glass is designed for micro-
gravity happy hour.
A D V A N C E D M A T E R I A L S & P R O C E S S E S | J U L Y / A U G U S T 2 0 1 6