
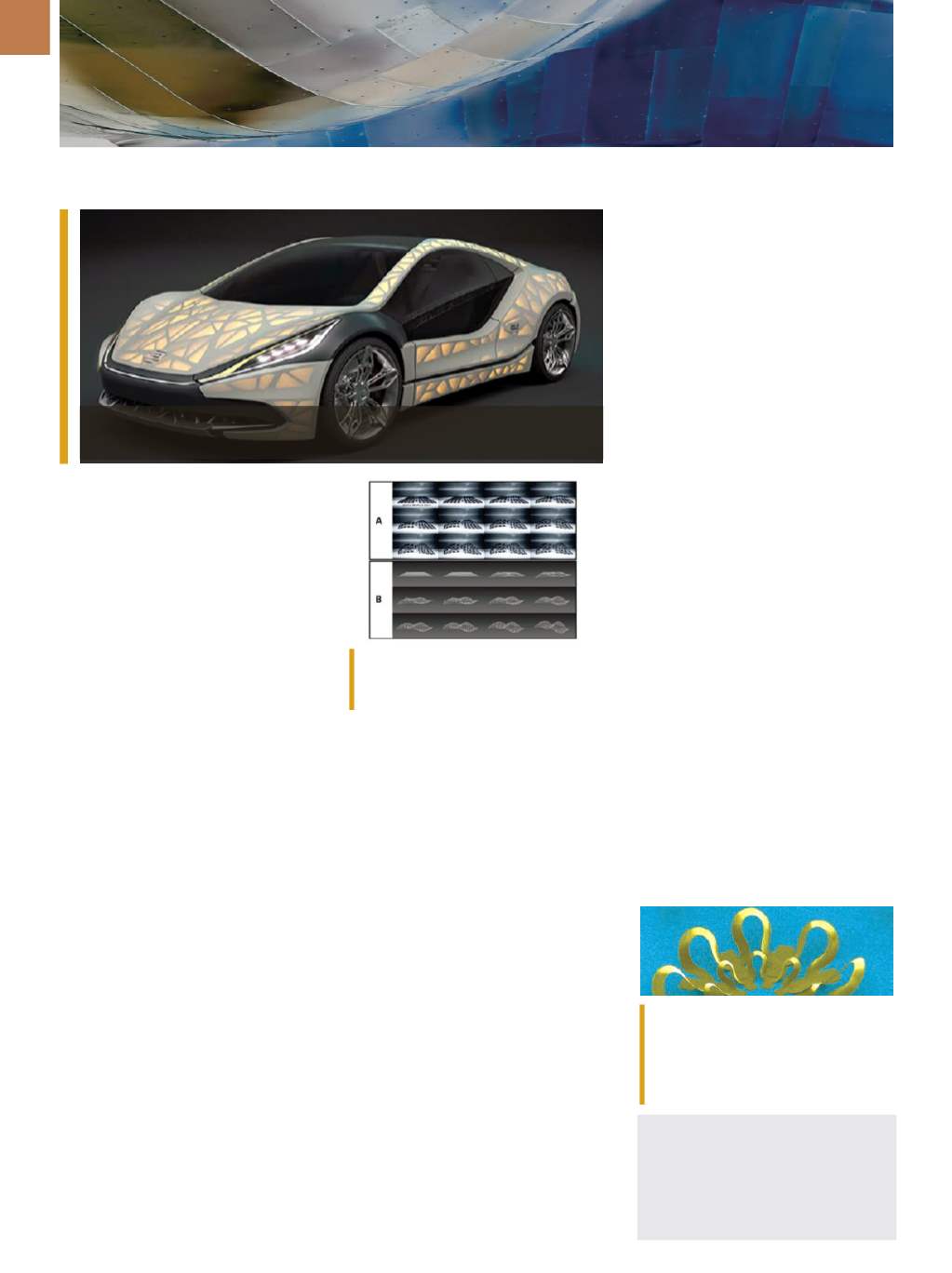
A D V A N C E D M A T E R I A L S & P R O C E S S E S | O C T O B E R 2 0 1 5
8
OMG!
OUTRAGEOUSMATERIALSGOODNESS
SPORTS CAR BOASTS
TEXTILE SKIN
EDAG, Germany, created a sports
car with a textile outer skin panel called
the Light Cocoon. It features weath-
erproof fabric skin stretched over a
3D-printed frame. The car also features
backlight technology, which illuminates
the skeleton-like, organic structure,
bringing the car to life, according to
company sources. The goal was to make
a lightweight and efficient car without
any waste. Instead of treating the body
as a closed surface, any material not
needed for the special load cases was
removed. Project partner Jack Wolfskin,
an outdoor wear and equipment manu-
facturer, supplied the stretchy weather-
proof fabric to serve as the outer body
skin. The sturdy material is four times
lighter than standard copier paper.
www.edag.de/en/edag.html.4D PRINTING BETTER THAN 3D?
A team of researchers at Massa-
chusetts Institute of Technology, Cam-
bridge, is taking 3D printing to a new
level with 4D methods. The goal of the
research is to 3D print items that are de-
signed to change shape after they are
printed. 3D printing technology uses a
wide range of materials to print objects,
such as plastic, ceramic, glass, metal,
chocolate, and even living cells.
The team used two different ma-
terials to print structures, one that was
a stiff plastic that did not bend and
another created by Stratasys, Edina,
Minn., that could absorb water and
double in volume when submerged.
The 3D-printed square grid measures
15 in. on all sides and could stretch and
fold when placed in water. Researchers
also printed a shape that resembles
the initials MIT and can turn into any
shape that resembles the initials SAL.
MIT mathematician Dan Raviv says the
technique has a variety of potential
uses, such as printing home applianc-
es, childcare products, and clothing
that could sense the environment to
perform better. Using 4D printing for
medical implants and cardiac stents is
another possibility.
For more informa-
tion: Dan Raviv, 617.324.0523,
darav@ mit.edu,
www.web.mit.edu.
POP-UP PRINTING OUTPER-
FORMS 3D METHODS
Researchers at Northwestern Uni-
versity,Evanston,Ill.,andtheUniversityof
Illinois at Urbana-Champaign developed
Are you working with or have you
discovered a material or its properties
that exhibit OMG - Outrageous
Materials Goodness?
Send your submissions to
Julie Lucko at
julie.lucko@asminternational.org.
The EDAG Light Cocoon features a weatherproof fabric skin stretched over a
3D-printed frame.
Researchers developed a simple fabrica-
tion technique that mimics the action of a
children’s pop-up book. An experimental
image of a flowerlike structure is shown
here. Courtesy of University of Illinois.
a new fabrication technique to create
complex 3D micro- and nanostructures.
The new method mimics the action of
a children’s pop-up book—starting as a
flat 2D structure and popping up into
a more complex 3D assembly. Using a
variety of advanced materials includ-
ing silicon, researchers produced more
than 40 different geometric designs, in-
cluding shapes resembling a peacock,
flower, starburst, table, basket, tent,
and starfish. “In just one shot you get
your structure,” says Northwestern’s
Yonggang Huang. “We first fabricate a
2D structure on a stretched elastic ma-
terial. Then we release the tension, and
a 3D structure pops up.” The pop-up
assembly technique outperforms 3D
printing on many levels and is expect-
ed to be useful in building biomedical
devices, sensors, and electronics. The
technique is fast and inexpensive and
can be used to build many different
structures at one time. It can also incor-
poratemany different materials, includ-
ing silicon. The method also enables
the incorporation of many materials
into one hybrid structure, the building
of structures on both micro- and nano
levels (down to a thickness of 100 nm),
and the production of a wide range of
geometries.
For more information: Yong-
gang Huang,
y-huang@northwestern. edu,
www.northwestern.edu.
When placed in water, a grid of 3D-printed,
water-absorbent material produces a broad
range of shapes with complex geometries.