
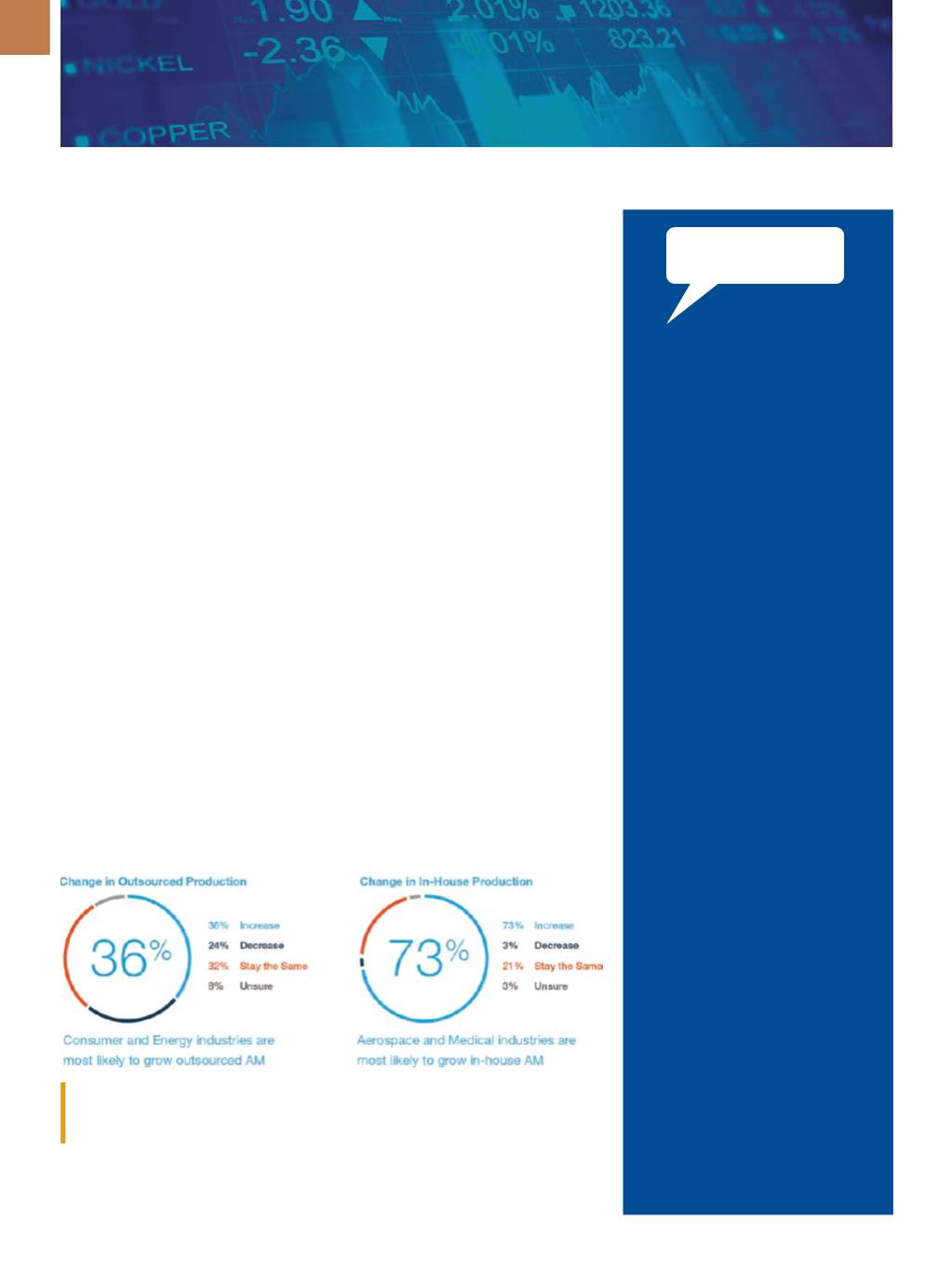
A D V A N C E D M A T E R I A L S & P R O C E S S E S | O C T O B E R 2 0 1 5
6
MARKET SPOTLIGHT
FEEDBACK
NEW REPORT HIGHLIGHTS 3D PRINTING TRENDS
A new report from Stratasys Direct
Manufacturing, Valencia, Calif.,
3D Print-
ing’s Imminent Impact on Manufactur-
ing,
provides an in-depth look at current
and emerging trends in additive man-
ufacturing (AM). The report is based on
an independent survey of 700 design-
ers, engineers, and executives—40%
of whom are employed by companies
with more than $50 million in revenue.
The majority of respondents, represent-
ing aerospace, automotive, consumer
products, and medical devices, say they
strongly believe more end-use parts will
be designed specifically for AM in the
near future. Further, additive metal use
is expected to nearly double over the
next three years.
Participants were asked what they
believe are the greatest benefits of
using AM. The most common responses
include more complex design capabili-
ties (79%), reduced lead time for parts
(76%), and improvements in manu-
facturing efficiency (42%). Respon-
dents were also asked about their
views on in-house production versus
outsourcing. With regard to the top
benefits of outsourcing, the most pop-
ular responses cite access to advanced
equipment and materials (73%), less
investment risk (60%), ability to pro-
duce parts not able to be manufactured
internally (53%), and access to AM
expertise (47%).
Survey takers were asked to share
their views on the top challenges faced
by their companies with regard to
using AM. Participants cite equipment
costs (63%), limited materials (54%),
post-processing requirements (39%),
and manufacturing costs (38%) as
today’s top concerns. As far as appli-
cations, respondents foresee a 36%
increase in tooling by 2018 and 38%
growth in end-use parts—with aero-
space and automotive expected to see
the largest increase. Participants were
also polled about which materials they
would like to see further developed
for AM: Top responses include metals
(84%), rubber-like materials (61%),
high temperature plastic (60%), and
carbon fiber (52%). To access the full
report, visit
pages.stratasysdirect.com/ trend-forecast.Participants were asked whether they expect their company’s in-house 3D printing produc-
tion to increase, decrease, or stay the same over the next three years, and were asked the
same question relative to outsourcing. Courtesy of Stratasys Direct Manufacturing.
MINIMILL MISTAKES
The recent article “Steel Minimills—
Part 1” (June issue) attributed the
supply of the continuous casting
machine at theNucor-Crawfordsville,
Indiana, facility to Siemens, which
is incorrect. This machine, and all
subsequent machines of this design
throughout the world, have been
furnished by SMS-Siemag AG, now
known as SMS Group. Also, the
second Nucor facility is located at
Hickman, Arkansas, not Iowa.
Bob Garness
MINIMILL MEMORIES
I read with great interest the article
“Steel Minimills: Part II” (July/August
issue). I was a full-time lab technician
at North Star Steel from 1972–75,
and then part-time from 1975–80
through college. By allowing me
to work during school, North Star
essentially financedmy B.S. degree
in metallurgical engineering at the
University of Minnesota and I’ll
always be grateful to them for that.
I was there when they built or pur-
chased a plant in Monroe, Michigan,
and also when they added a car
shredder and an epoxy coating group
for their rebar. Every once in a while,
I drive by the plant and wonder what
happened to North Star and if they
are as big as they used to be. Judging
from your article, I guess not. Thanks
again for the interesting history. It
was a pleasure reading about the
good ol’ days in the steel business.
Steve Nelson
We welcome all comments and
suggestions. Send letters to
frances. richards@asminternational.org.