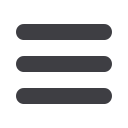
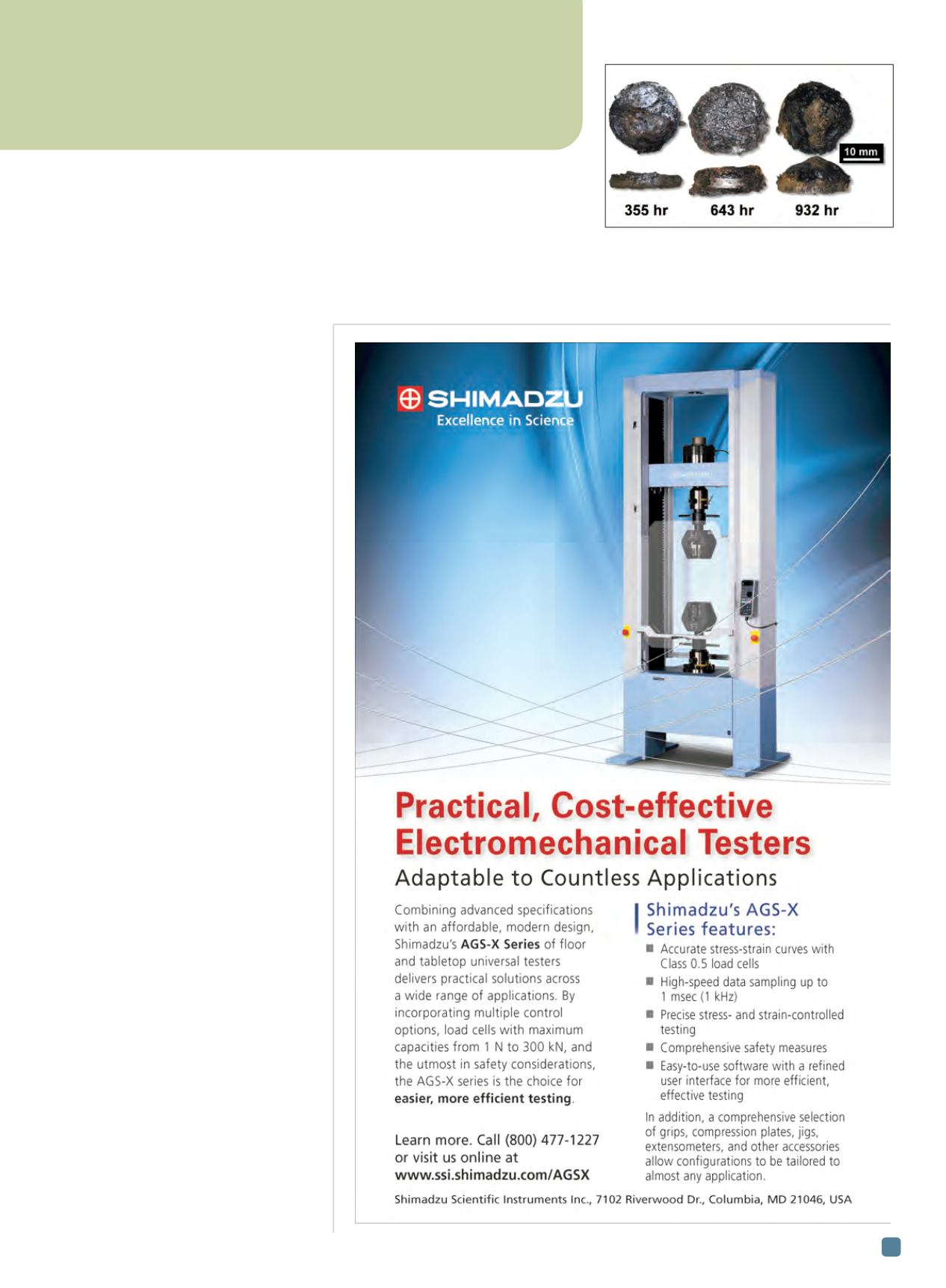
ADVANCED MATERIALS & PROCESSES •
SEPTEMBER 2014
11
Study points to impending corrosion failures at gas stations
According to the National Institute of Standards and Technology (NIST),
Gaithersburg, Md., a hidden hazard lurks beneath many of the roughly 156,000 gas
stations across the U.S.—corrosion in parts of underground gas storage tanks that
could result in failures, leaks, and groundwater contamination. In recent years, field
inspectors in nine states have reported many rapidly corroding gas storage tank
components such as sump pumps. The
incidents are generally associated with use
of gasoline-ethanol blends and the pres-
ence of bacteria that convert ethanol to
acetic acid, a component of vinegar.
Following these findings, a NIST lab-
oratory study demonstrated severe corro-
sion—rapidly eating through 1 mm of wall
thickness per year—on steel alloy samples
exposed to ethanol and acetic acid vapors.
Gas stations may need to replace sub-
mersible pump casings, typically made of
steel or cast iron, sooner than expected.
Such retrofits could cost an estimated
$1500 to $2500 each. The study focused
only on sump pump components, located
directly below access covers at filling sta-
tions. The pumps move fuel from under-
ground tanks to fuel dispensers.
Much of the U.S. fuel infrastructure
was designed for unblended gasoline.
However, ethanol is now widely used as a
gasoline additive due to its oxygen content
and octane rating. For the study, re-
searchers developed new test methods
and equipment to examine copper and
steel alloy samples either immersed in
ethanol-water solutions inoculated with
bacteria, or exposed to the vapors above
the medium. Corrosion rates were meas-
ured over 30 days.
The study confirmed damage similar
to that seen on sump pumps by field in-
spectors. The worst damage was found on
steel exposed to the vapors. Copper in
both the liquid and vapor environments
also sustained damage, but corrosion
rates were slower. Although slower, local-
ized corrosion was observed on cold-
worked copper, used in sump pump
tubing. Stress-corrosion cracking is a con-
cern for bent copper tubing because it
would greatly reduce tube lifetime and re-
sult in leaks. Test equipment developed
for the study could be used in future in-
vestigations of special coatings and bio-
cides or other ways to prevent failures and
leaks.
nist.gov.Optical micrographs of severe corrosion on steel
alloy samples exposed to ethanol and acetic acid
vapors—conditions typical of underground gas
storage tanks—after 355 hours, 643 hours, and
932 hours. Courtesy of NIST.