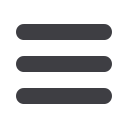
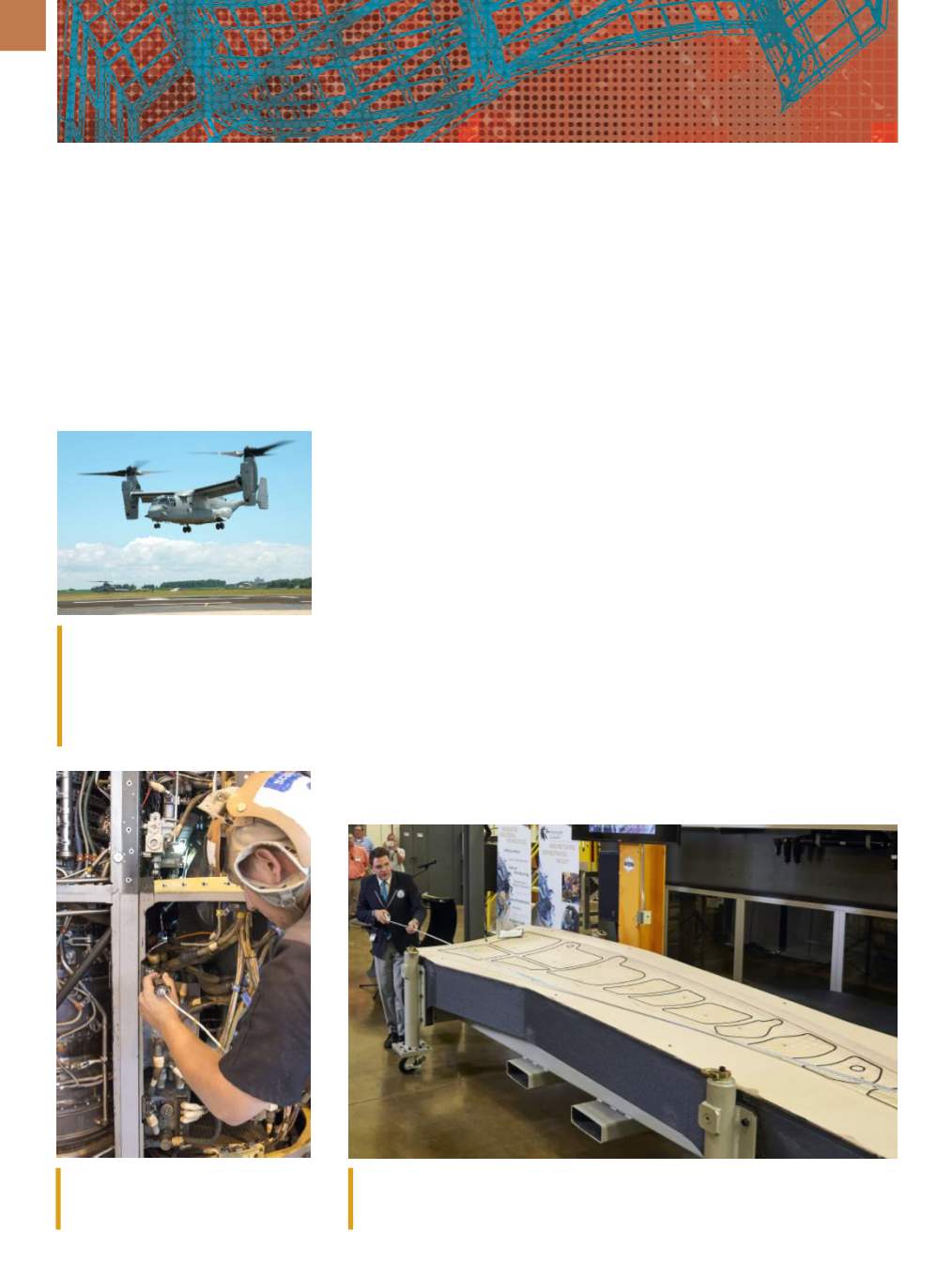
6 4
A D V A N C E D M A T E R I A L S & P R O C E S S E S | O C T O B E R 2 0 1 6
3D PRINTSHOP
PRINTED COMPONENT
ACES FLIGHT TEST
Naval Air Systems Command,
Patuxent River, Md., completed its first
successful flight test of a safety-crit-
ical aircraft component produced
by additive manufacturing (AM). The
component, a titanium link and fit-
ting assembly 3D printed at Naval Air
An MV-22B Osprey equipped with a
3D-printed titanium link and fitting inside
an engine nacelle maintains a hover
during a July 29 demonstration at Patux-
ent River Naval Air Station, Md. Images
courtesy of U.S. Navy.
Warfare Center Aircraft Division, Lake-
hurst, N.J., is one of four that secure
a V-22’s engine nacelle to the primary
wing structure. It will remain on the
test aircraft—an MV-22B Osprey—for
continued evaluation. Prior to this
flight, multiple V-22 components built
at Lakehurst and at Penn State Applied
Research Laboratory, Arlington, Va.,
were tested at Patuxent.
“AM is a game changer,” says Liz
McMichael, AM Integrated Product
Team lead. “We’ll be working with V-22
to go from this first flight demonstra-
tion to a formal configuration change
to use these parts on any V-22 aircraft.”
McMichael and her team have identi-
fied six safety-critical parts they plan
to build and test over the next year for
three U.S. Marine Corps rotorcraft plat-
forms including the V-22, H-1, and CH-
53K. Three of the parts will be made
out of titanium, while the other three
will be stainless steel. Naval aviation
has employed additive manufacturing
as a prototyping tool since the early
1990s and has recently begun print-
ing non-flight-critical parts and tools.
navy.mil.GUINNESS RECORD HOLDER
HEADS TOBOEING
A trim-and-drill tool, developed
by researchers at the DOE’s Oak Ridge
National Laboratory (ORNL), Tenn., was
named the largest solid 3D-printed item
by Guinness World Records. Measuring
17.5 x 5.5 x 1.5 ft and weighing approx.
1650 lb, the tool will be tested for use
in building the Boeing 777X passen-
ger jet. “The more expensive metallic
tooling option we currently use comes
from a supplier and typically takes three
months to manufacture using conven-
tional techniques,” says Leo Christodou-
lou, Boeing’s director of structures and
materials. The new tool was printed on
ORNL’s Big Area Additive Manufacturing
machine in just 30 hours using carbon
fiber and ABS thermoplastic composite
materials. After ORNL completes verifi-
cation testing, Boeing plans to use the
record-setting trim-and-drill tool in its
new St. Louis production facility to se-
cure the jet’s composite wing skin for
drilling and machining before assembly,
providing feedback toORNL on the tool’s
performance along the way.
ornl.gov.Aviation mechanic Cody Schwarz works
to install the 3D-printed link and fitting on
the MV-22B Osprey engine nacelle.
Official measurement of the 3D-printed trim tool co-developed by ORNL and Boeing exceed-
ed the requiredminimum size to achieve the Guinness World Records title of largest solid
3D-printed item.