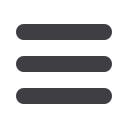
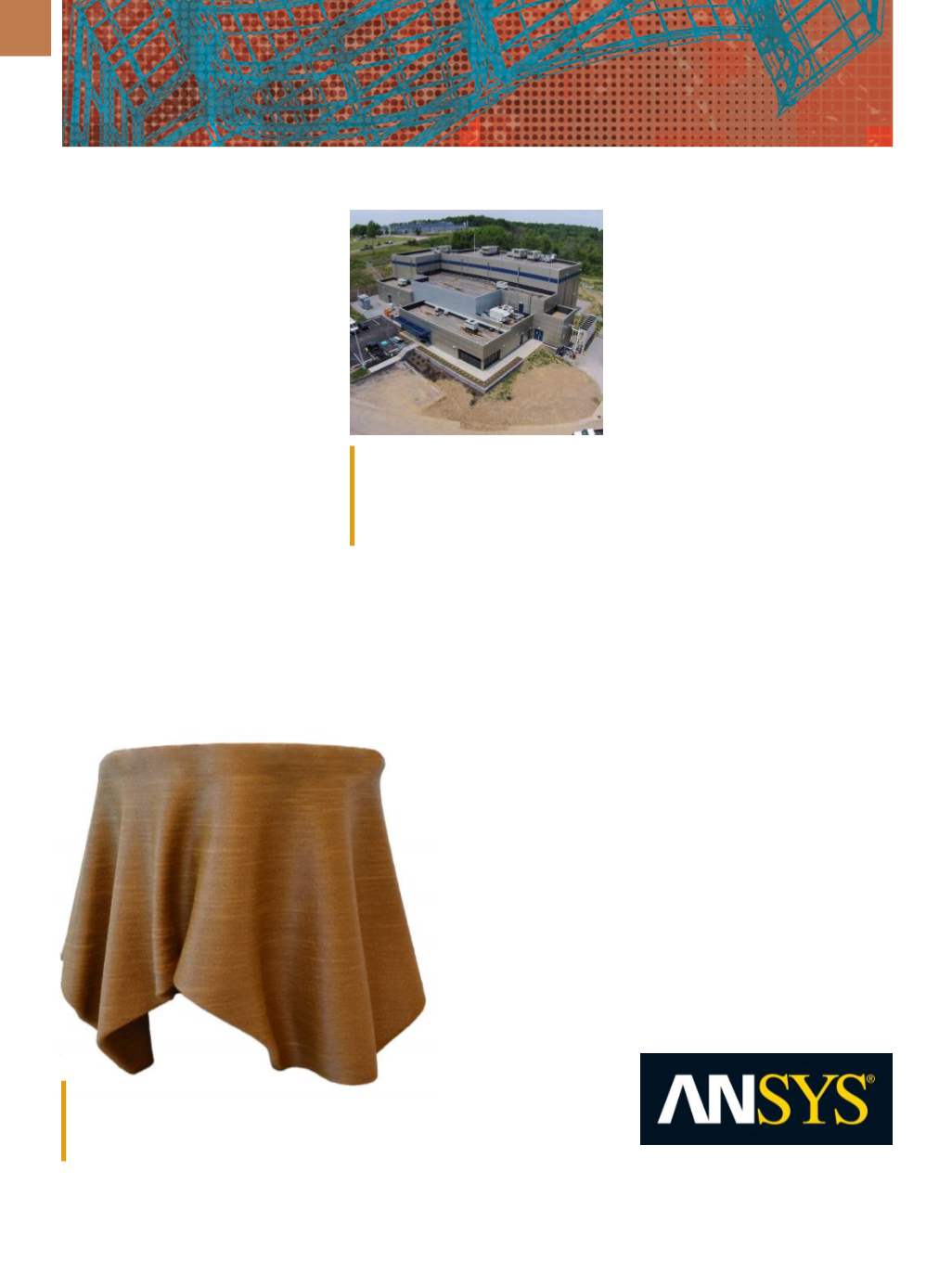
6 4
A D V A N C E D M A T E R I A L S & P R O C E S S E S | S E P T E M B E R 2 0 1 6
3D PRINTSHOP
BAMBOO BOOSTS
SUSTAINABILITY
Researchers at Oak Ridge Nation-
al Laboratory, Tenn., are using bamboo
fiber in 3D-printing experiments to de-
termine whether bio-based feedstock
materials are feasible in additive manu-
facturing. Chopped bamboo fibers were
added to a bio-polymer resin to create
bamboo-based pellets, resulting in a
more sustainable material that can be
used for manufacturing molds, proto-
types, appliances, and furniture. In one
experiment, a table that contains 10%
bamboo fiber composite was 3D-print-
ed. “We are investigating the use of
different types of cellulose fibers to
develop feedstock materials with bet-
ter mechanical performance that can
increase the number of available com-
posites and opportunities for sustain-
able practices,” explains Soydan Ozcan,
R&D scientist.
For more information:
Soydan Ozcan, 865.241.2158, ozcans@
ornl.gov,
www.ornl.gov.
ALCOA OPENS METAL
POWDER FACILITY
Alcoa Inc., Pittsburgh, recently
opened a state-of-the-art, 3D-printing
metal powder production facility. Lo-
cated at the Alcoa Technology Center
near Pittsburgh, the company will pro-
duce titanium, nickel, and alu-
minum powders optimized for
3D-printed aerospace parts. Al-
coa has also invested in a range
of technologies to further
develop additive processes,
product design, and qualifi-
cation. The facility will form
part of Arconic following
separation from Alcoa’s tra-
ditional commodity busi-
ness in the second half of
2016. The plant is part of
a $60 million investment
in advanced 3D-printing
materials and processes
that builds on the company’s
capabilities in California, Geor-
gia, Michigan, Pennsylvania, and
Texas. In addition to producing pow-
ders, Alcoa is focused on advancing a
range of additive techniques, including
its Ampliforge process that combines
additive and traditional manufacturing.
With this new technique, a nearly com-
plete 3D part is printed then finished
with another process such as forging.
alcoa.com.
PARTNERSHIP TO DEVELOP
COMPUTING TOOLS
A new collaboration between
Ansys Inc., Pittsburgh, and the Uni-
versity of Pittsburgh (Pitt) aims to
solve some of the industry’s toughest
additive manufacturing (AM) problems.
Printing metal is particularly challeng-
ing because it involves lasers, which op-
timize density but can also melt metal
in unexpected ways. In addition, rapid
heating and cooling creates stresses
that can deform the end product. Ansys
and Pitt are working together to simu-
late those deformations before printing
to ensure products have the desired
shape and perform as expected. As part
of the collaboration, the university is
opening a 1200-sq-ft Ansys Additive
Manufacturing Research Laboratory
in the Swanson School of Engineering.
The new facility will also support fac-
ulty and students conducting collab-
orative research with Ansys and other
industry partners, including those in
the biomedical, aerospace, and defense
industries. Lab workers will have access
to a variety of Ansys software, enabling
them to explore, simulate, and analyze
solutions for stress and fatigue on criti-
cal components designed for the auto-
motive, aerospace, and medical device
industries.
ansys.com.
A 3D-printed table was manufactured
using 10% bamboo fiber, an initial step
toward sustainable practices using
bio-derivedmaterials.
Alcoa opened a state-of-the-art, 3D-
printing metal powder production
facility located at the Alcoa Technology
Center near Pittsburgh. Courtesy of
Business Wire.