
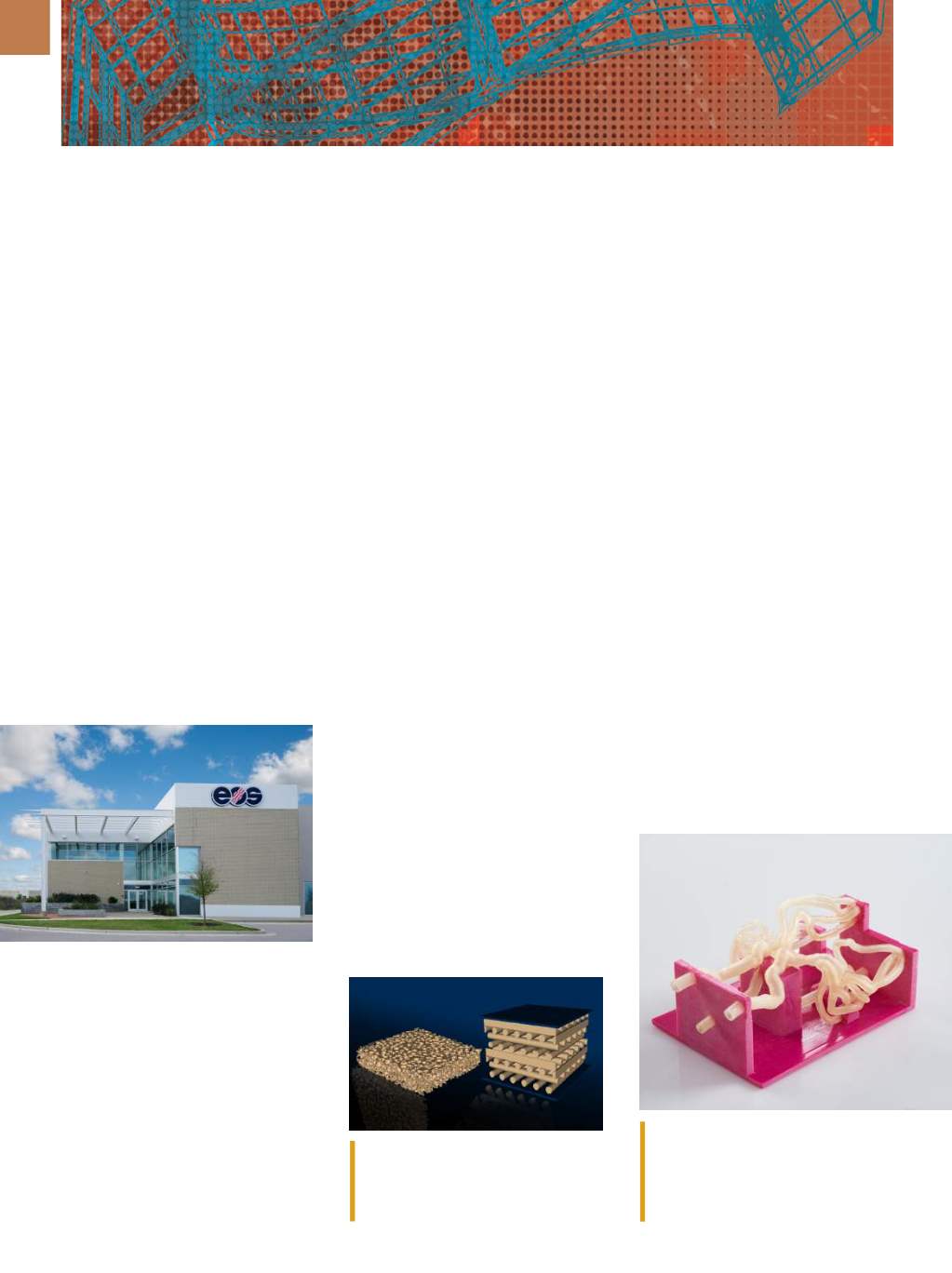
7 6
A D V A N C E D M A T E R I A L S & P R O C E S S E S | J U N E 2 0 1 6
3D PRINTSHOP
E
OS, Germany, celebrated the grand
opening of its newest U.S. facility
in Pflugerville, Texas, in early May.
The new location primarily provides
increased service and support for the
company’s growing North America mar-
ket, which topped $100 million in 2015.
The site features an innovations labora-
tory (iLab), where application engineers
interact directly with customers, a show-
room that displays the company’s addi-
tive manufacturing (AM) systems, and
an AM Ventures division to help support
start-up ideas. EOS Materials, also known
as Advanced Laser Materials (ALM),
will remain in Temple, Texas. This facil-
ity produces polymer powder for both
EOS systems and other powder-based
AM technologies. The Novi, Mich., site
continues to be an important regional
technical center for the company. Future
U.S. expansion plans include Boston and
Northern California.
eos-na.com.
EOS OPENS TEXAS FACILITY
rubber (i.e., elastomer) comprising
each foam showed the opposite effect,
as the rubber in the printed material
aged faster than the corresponding
rubber used in the traditional foam.
llnl.gov.NEW CENTER SUPPORTS
MEDICAL APPLICATIONS
Stratasys Ltd., Minneapolis, is
partnering with the Jacobs Institute,
Buffalo, N.Y., to create a new center of
excellence to advance the use of 3D
printing for a variety of medical appli-
cations. The center will use Stratasys’
3D printing technology to develop
and test new medical devices using
3D-printed prototypes and models, as
well as enrich clinical education and
training. The facility will also serve as a
referral center for hospitals and medi-
cal research organizations considering
3D printing labs. Stratasys will collabo-
rate with Jacobs on technical and clini-
cal case studies that include 3D-printed
applications and will also provide
financial support for vital research proj-
ects.
stratasys.com.
Microstructures of two different foam
materials. Left, traditional open-cell sto-
chastic foam; right, 3D-printed foamwith
face-centered tetragonal lattice structure.
with significant dispersion in cell size,
shape, thickness, connectedness, and
topology. As an alternative, a team
at LLNL’s additive manufacturing lab
recently demonstrated the feasibility
of 3D printing uniform foam structures
through a process called direct-ink-
write. However, because 3D printing
requires the use of polymers of certain
properties, it is important to under-
stand the long-term mechanical stabil-
ity of such printedmaterials before they
can be commercialized. This is espe-
cially vital in applications such as sup-
port cushions, where the foammaterial
is subjected to long-term mechanical
stresses.
To address the stability ques-
tion, accelerated aging experiments
in which samples of both traditional
stochastic foam and 3D-printed mate-
rials were subjected to elevated tem-
peratures under constant compressive
strain were performed. The stress
condition,
mechanical
response,
and structural deformation of each
sample were monitored for one year
or longer. A method called time-
temperature-superposition was then
used to model the evolution of such
properties over a period of decades
under ambient conditions. The study
shows that 3D-printed materials age
slowly compared to their traditional
counterparts. Interestingly, the native
3D-PRINTED FOAM
OUTPERFORMS STANDARD
MATERIALS
Scientists at Lawrence Livermore
National Laboratory (LLNL), Calif., dis-
covered that 3D-printed foam works
better than standard cellular materials
in terms of durability and long-term
mechanical performance. Traditionally,
foams are created by processes that
lead to a highly nonuniform structure
Vascular testing model used to validate
newmedical devices that treat brain
aneurysms, produced on the Stratasys
Objet500 Connex3 3D Printer. Courtesy
of Jacobs Institute.