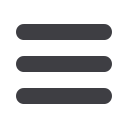
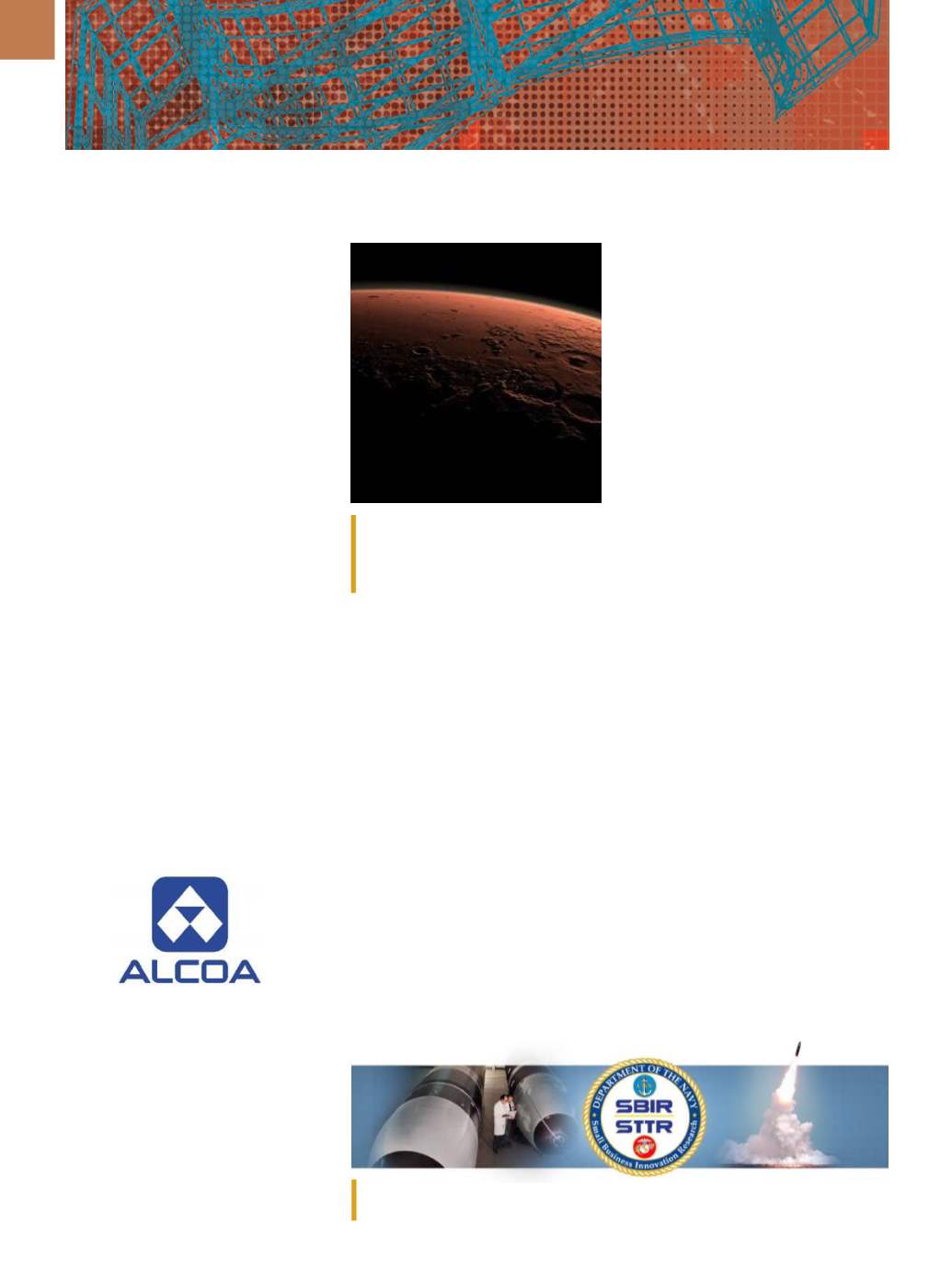
4 8
A D V A N C E D M A T E R I A L S & P R O C E S S E S | M A Y 2 0 1 6
3D PRINTSHOP
A
lcoa, Pittsburgh, will supply 3D-
printed titanium fuselage and
engine pylon components for
irbus commercial aircraft, delivering
the first additively manufactured (AM)
parts to Airbus in mid-2016. According
to company sources, the agreement
will draw on Alcoa’s aerospace experi-
ence as well as new technologies gained
through the recent acquisition of RTI
International Metals Inc. and organic
expansion in Whitehall, Mich. Last year,
Alcoa acquired RTI, now known as
Alcoa Titanium & Engineered Products
(ATEP), which grew Alcoa’s AM capa-
bilities to include 3D-printed titanium
and specialty metals parts produced at
ATEP’s Austin, Texas, facility. The Airbus
agreement will use these capabilities
as well as ATEP’s titanium ingot melt-
ing and billetizing, machining, finishing,
and inspection technologies. Alcoa will
also use advanced CT scan and hot iso-
static pressing (HIP) capabilities at its
aerospace facility in Michigan. Addition-
ally, Alcoa is bolstering its AM capabili-
ties through a $60 million expansion in
advanced 3D-printing materials and pro-
cesses, including metallic powders. The
expansion is located at the Alcoa Tech-
nical Center near Pittsburgh.
alcoa.com.
SELECTIVE SEPARATION
SINTERING WINS NASA
CHALLENGE
A new 3D-printing process called
selective separation sintering (SSS),
developed by Behrokh Khoshnevis
of the University of Southern Califor-
nia (USC), won first place in the NASA
In-Situ Materials Challenge due to
its breakthrough application in the
ALCOA TO SUPPLY 3D-PRINTED PARTS TO AIRBUS
while the SSS is a powder-based tech-
nique that is suitable for constructing
smaller-scale objects such as bricks,
interlocking tiles, and a number of
functional objects such as metallic
components. Khoshnevis’ teamwill test
the SSS process in a vacuum chamber
of USC’s Astronautics Rocket Lab and
NASA’s Kennedy Space Center facilities.
nasa.gov, u sc.edu.
NAVY GRANTS MISSILE
SYSTEM CONTRACT TO MTI
The U.S. Navy recently granted
Metal Technology (MTI), Albany, Ore.,
a contract to develop advanced aero-
space additive manufacturing tech-
niques for low-cost manufacturing of
refractory metal components for mis-
sile propulsion systems used on the
Trident D5 missile system. While the
Trident system is expected to remain
in service until 2042, current manufac-
turing techniques for refractory metal
components of the propulsion system
are complex and labor intensive. MTI
will work with the Navy to reduce cost
using advanced additive manufactur-
ing to fabricate refractory metal parts
with significant reductions in com-
plexity. “Phase one of this project is to
develop processes and demonstrate
the fabrication of simplified, sub-scale
articles using C103 Niobium alloy and
provide approaches for fabrication of
additional refractory metals and alloys
including molybdenum and tantalum,”
says CEO Gary Cosmer.
mtialbany.com.
Metal Technology is moving forward with advanced technology to support the Trident II
missile program.
construction of physical structures in
space. Khoshnevis is director of the
Center for Rapid Automated Fabrica-
tion Technologies at the USC Viterbi
School of Engineering. His team used
a synthetic material similar to those
found on Mars to formulate a robotic
fabrication process, which employs
high melting-point ceramics, such
as magnesium oxide, to create tiles
capable of withstanding the pressure
and heat of exhaust plumes of land-
ing spacecraft. The SSS process uses
Khoshnevis’ existing contour crafting,
a large-scale 3D printing method that
won the 2014 NASA competition grand
prize. However, the contour crafting
is an extrusion-based 3D printing
method and is mainly suited for large-
scalemonolithic structure construction,
The NASA In-Situ Materials Challenge
competition mandated that competitors
use materials found on Mars. Courtesy of
NASA.