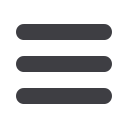
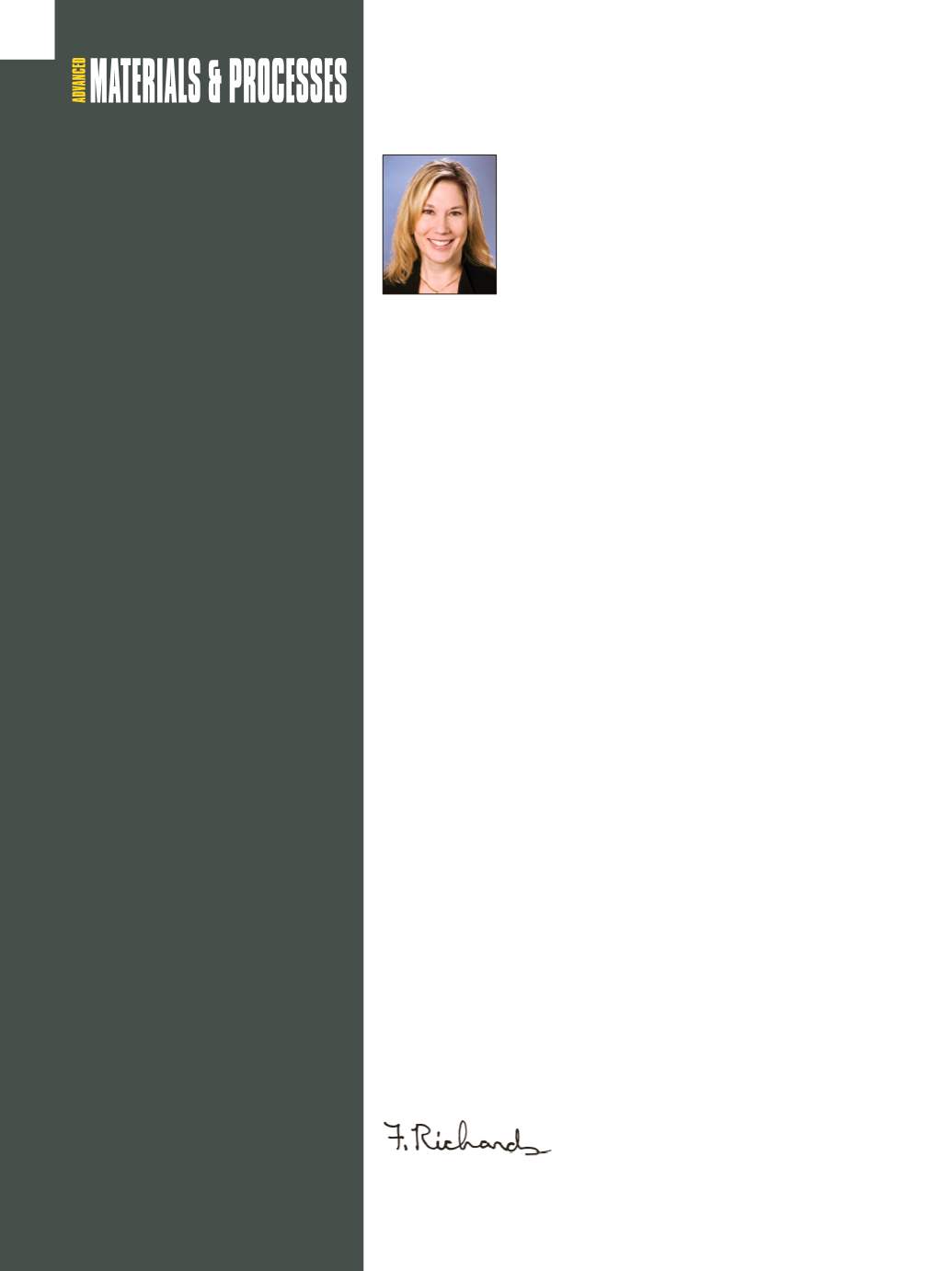
4
A D V A N C E D M A T E R I A L S & P R O C E S S E S | M A Y 2 0 1 6
ASM International
9639 Kinsman Road, Materials Park, OH 44073
Tel: 440.338.5151 • Fax: 440.338.4634
Frances Richards,
Editor-in-Chief
frances.richards@asminternational.orgJulie Lucko,
Editor
julie.lucko@asminternational.orgEd Kubel and Erika Steinberg,
Contributing Editors
Jim Pallotta,
Creative Director
jim.pallotta@asminternational.orgKate Fornadel,
Layout and Design
Annie Beck,
Production Manager
annie.beck@asminternational.orgPress Release Editor
magazines@asminternational.orgEDITORIAL COMMITTEE
Jaimie Tiley,
Chair,
U.S. Air Force Research Lab
Somuri Prasad,
Vice Chair,
Sandia National Lab
Yu-Ping Yang,
Past Chair,
EWI
Ellen Cerreta,
Board Liaison,
Los Alamos
National Lab
Steven Claves,
Alcoa Technical Center
Mario Epler,
Carpenter Technology Corp.
Adam Farrow,
Los Alamos National Lab
Nia Harrison,
Ford Motor Co.
Yaakov Idell,
NIST
John Shingledecker,
EPRI
Kumar Sridharan,
University of Wisconsin
ASMBOARDOF TRUSTEES
Jon D. Tirpak,
President
William E. Frazier,
Vice President
Sunniva R. Collins,
Immediate Past President
Craig D. Clauser,
Treasurer
Ellen K. Cerreta
Kathryn Dannemann
Ryan M. Deacon
Jacqueline M. Earle
John R. Keough
Zi-Kui Liu
Sudipta Seal
Tirumalai S. Sudarshan
David B. Williams
Tom Dudley,
Interim Managing Director
STUDENT BOARDMEMBERS
Aaron Birt, Joseph DeGenova, Sarah Straub
Individual readers of Advanced Materials & Processes may,
without charge, make single copies of pages therefrom for per-
sonal or archival use, or may freely make such copies in such
numbers as are deemed useful for educational or research
purposes and are not for sale or resale. Permission is granted
to cite or quote fromarticles herein, provided customary
acknowledgment of the authors and source is made.
The acceptance and publication of manuscripts in Advanced
Materials & Processes does not imply that the reviewers,
editors, or publisher accept, approve, or endorse the data,
opinions, and conclusions of the authors.
A
s I write this column, I am in the middle of a press
visit to Germany built around the theme of Indus-
try 4.0, the German name for what Americans call
the Industrial Internet. These two terms essentially define
the same idea—merging the physical world with the virtual
world of the Internet and software. As part of this techno-
logical tour across Deutschland, the DFKI—German Re-
search Center for Artificial Intelligence (AI)—demonstrated
an Industry 4.0 system at Hannover Messe, the world’s largest industrial fair. The
modular SmartFactoryKL system showcases ideas such as plug and produce,
predictivemaintenance, zero-downtimemaintenance, scalable automation, and
mix-and-match machine modules collaborating in a production environment.
Detlef Zühlke, DFKI’s scientific director, explained how the Industry 4.0
world will be covered in intelligent sensors, enabling highly dynamic, automat-
ed cyber-physical systems, in which much of the intelligence lives in the cloud
rather than individual physical components. Central controllers will be relics of
the past. Instead, modular production units (think of Lego bricks with specific
tasks) will self-identify once they are plugged into the larger system, commu-
nicate what they can do, and then autonomously network with other machine
units to accomplish different jobs. Zühlke believes this model is likely five years
away from widespread industry adoption. One reason for the delay is that in-
ternational standards still need to be developed so systems can work together
seamlessly. In the U.S., we have a newer entity called the Digital Manufactur-
ing and Design Innovation Institute (DMDII), Chicago, working on similar goals.
DMDII is a federally funded R&D organization that “encourages factories across
America to deploy digital manufacturing and design technologies, so those fac-
tories can become more efficient and cost-competitive.”
In other advanced manufacturing news, GE’s breathtaking and ambitious
Center for Additive Technology Advancement (CATA) opened a few weeks ago
near Pittsburgh. The $39 million, 125,000-sq-ft facility is designed as a regional
innovation hub to support GE’s eight business segments. Key additive manufac-
turing (AM) technologies showcased at the new center include direct metal laser
melting, fused deposition modeling, laser hot wire, poly jet, and sand binder
jetting. CATA will work with other organizations such as printer suppliers, uni-
versities including nearby Carnegie Mellon, and institutes like America Makes to
develop AM technologies and best practices.
CEO Jeff Immelt was on hand to commemorate the opening. He says we are
only in the “first 15 minutes of this industry” and leadership is still up for grabs.
With more than 400 AM machines in service across GE, the company is planning
to build on the stunning success of its 3D-printed jet engine fuel nozzles. Immelt
added that the company hopes to make as much as 25% of its products using AM
over the next few years—an ambitious goal.
It seems clear that a manufacturing revolution is now in full swing, with AI
and AM as key technologies. From aerospace and automotive components to
consumer goods and medical products, every industry will be transformed. We
hope you will stay tuned to
AM&P
to keep informed about how these changes will
impact the materials community.
frances.richards@asminternational.orgAI AND AM CHANGING THE
INDUSTRIAL LANDSCAPE