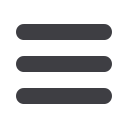
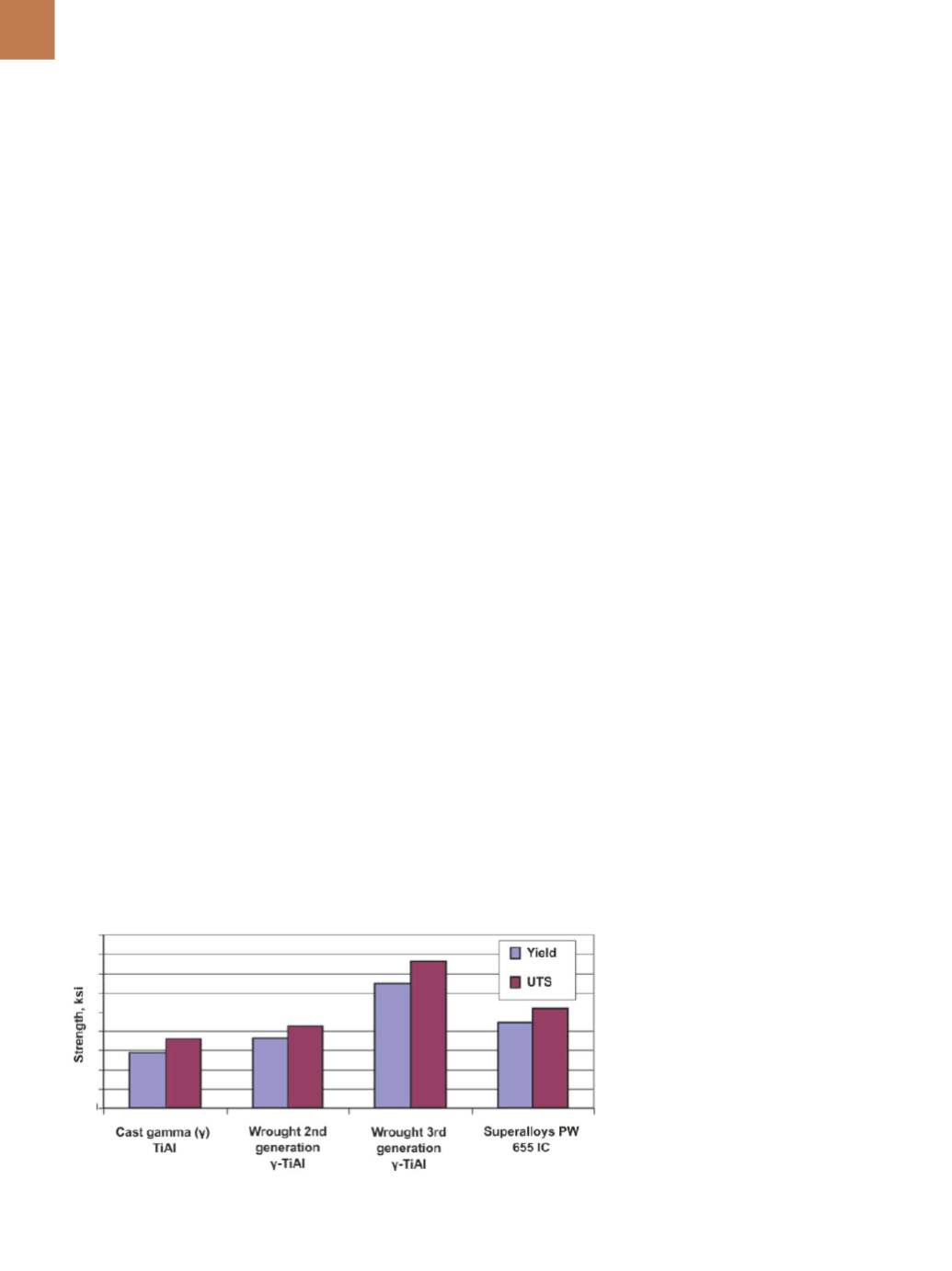
A D V A N C E D M A T E R I A L S & P R O C E S S E S | M A Y 2 0 1 6
3 8
containing a small amount of
chromium to enrich palladium and
ruthenium on the corroded surface
resulting from selective dissolution
of titanium.
•
Ti-0.5Al-0.35Si (Ti-0.9SA) and
Ti-0.5Al-0.45Si-0.2Nb (Ti-1.2ASN),
which achieve high-temperature
oxidation resistance to 750
°
C via a
combination of aluminum, silicon,
and niobium additions. Also, the
formation of silicides in the matrix
inhibit grain growth.
•
Ti-4.5Al-2Mo-1.6V-0.5Fe-0.3Si-
0.03C (Ti-9), a cold-rolled alloy,
and Ti-4.5Al-4Cr-0.5Fe-0.2C (EL-F),
a forgeable alloy with carbon for
improved high temperature strength.
•
Ti-2Al-1Sn-1Fe-1Cu-0.5Cr-0.3Si
(Ti-2111S), a near-alpha alloy con-
taining low-cost alloying elements
designed for sheet products, which
exhibits lower levels of anisotropic
properties and improved superplas-
tic properties.
Allegheny Technologies Inc. (ATI),
Pittsburgh, and Timet Metals Corp.,
Exton, Pa., developed new
α
+
β
alloys
with improved superplastic forming
(SPF) capability. TIMETAL 54M, or Ti-54M
(Ti-5Al-4V-0.75Mo-0.5Fe), demonstrates
SPF capability at temperatures as low
as 775°C, providing a significant cost
benefit during SPF processing. ATI 425
(Ti-4Al-2.5V-1.5Fe-0.25O) exhibits excel-
lent cold and hot workability, and can
be produced in various forms from coil
to forged products with SPF properties
similar to Ti-54M.
RTI International Metals Inc., Pitts-
burgh, developed a heat treatable
α
+
β
alloy, RTI-XPT (5.5Al-4.3 Zr-5.7V-1.3
Mo-0.10O2-0.06Pd), to compete with
Grade 29 titanium for use in highly
stressed tubular applications used in
high-pressure and high-temperature
corrosive environments. Its corrosion
resistance makes it suitable for sour
and sweet aerated and de-aerated
chloride media at temperatures up to
290°C. RTI-XPT is approved for sour ser-
vice under the ANSI/NACE MR01750/ISO
15156 Standard.
Timet also developed a new tita-
nium alloy for the chemical process
industry targeted for use in aggressive
environments severe enough to require
palladium or rhenium alloys or high-
end industrial nickel alloys. Corrosion
resistance of the new carbon-bearing
alloy is similar to, or better than, that of
the alloys previously mentioned. Mate-
rial costs are dramatically reduced by
not using expensive alloying elements.
Dynamet Techology Inc., Burling-
ton, Mass., developed CermeTi-10, a
titanium carbide particle-reinforced
titanium alloy for die-cast shot sleeve
liners. The alloy reportedly increases
sleeve life up to 20 times longer,
enables three times longer plunger tip
life, reduces maintenance costs, and
results in fewer defects and decreased
lubrication requirements. These lower
cost, lightweight Al components further
enable their use by the auto industry to
meet the federal government’s increas-
ingly strict standards for improved fuel
economy. In a cooperative effort with
Medtronic Inc., Dynamet used another
CermeTi alloy containing particulates
to fabricate the Prestige LP Disc, an
artificial cervical disc. These compo-
nents have been used in Europe since
2004 and are now approved for use in
the U.S. They have a lower wear rate and
produce less scatter on post-operative
MRI scans than stainless steel.
Next-generation aeroengine archi-
tectures challenge the properties of
traditional materials with higher engine
core temperatures and turbine speeds,
which led to development of a third-gen-
eration
γ
-phase containing Ti-aluminide
alloy (Fig. 2). Alloy TNM combines good
processability with required mechanical
properties, resulting in the first appli-
cation of forged
γ
-TiAl turbine blades
jointly developed by Pratt &Whitney and
MTU Aero Engines, Munich.
NEW CHARACTERIZATION
METHODS
Advanced characterization meth-
ods such as atomic-force spectroscopy
(AFS), high resolution digital image
correlation (DIC), and scanning trans-
mission electron microscopy (STEM)
provide the means to understand phase
transformations and deformationmech-
anisms under a variety of external condi-
tions. These techniques were discussed
during several conference sessions.
For example, researchers at Univer-
sity of Manchester, UK, are combining
electron backscatter diffraction (EBSD)
orientation maps and high resolution
DIC to observe nanoscale strain behav-
ior in Ti-6Al-4V with varying degrees
of microtexture. Two extreme micro-
structures show noticeable differences
in strain heterogeneity, with the strong
microtexture sample exhibiting a higher
density of slip traces with increased
maximum shear strains. Nanoscale
deformation studies provide more
detailed insight into the actual extent of
the strain heterogeneity, with maximum
shear strain intensities of approximately
10 times the applied strain.
Spatially resolved acoustic spec-
troscopy (SRAS), a laser-basedultrasonic
method that resolves crystal orientation
in titanium, was developed at Univer-
sity of Nottingham, UK. The technique
is based on local surface acoustic wave
velocity in different directions to image
Fig. 2 —
Comparison of room-temperature strength of third-generation forged
γ
-TiAl alloy with
other materials used as low-pressure turbine blades in the PW1000G engine.