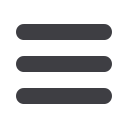
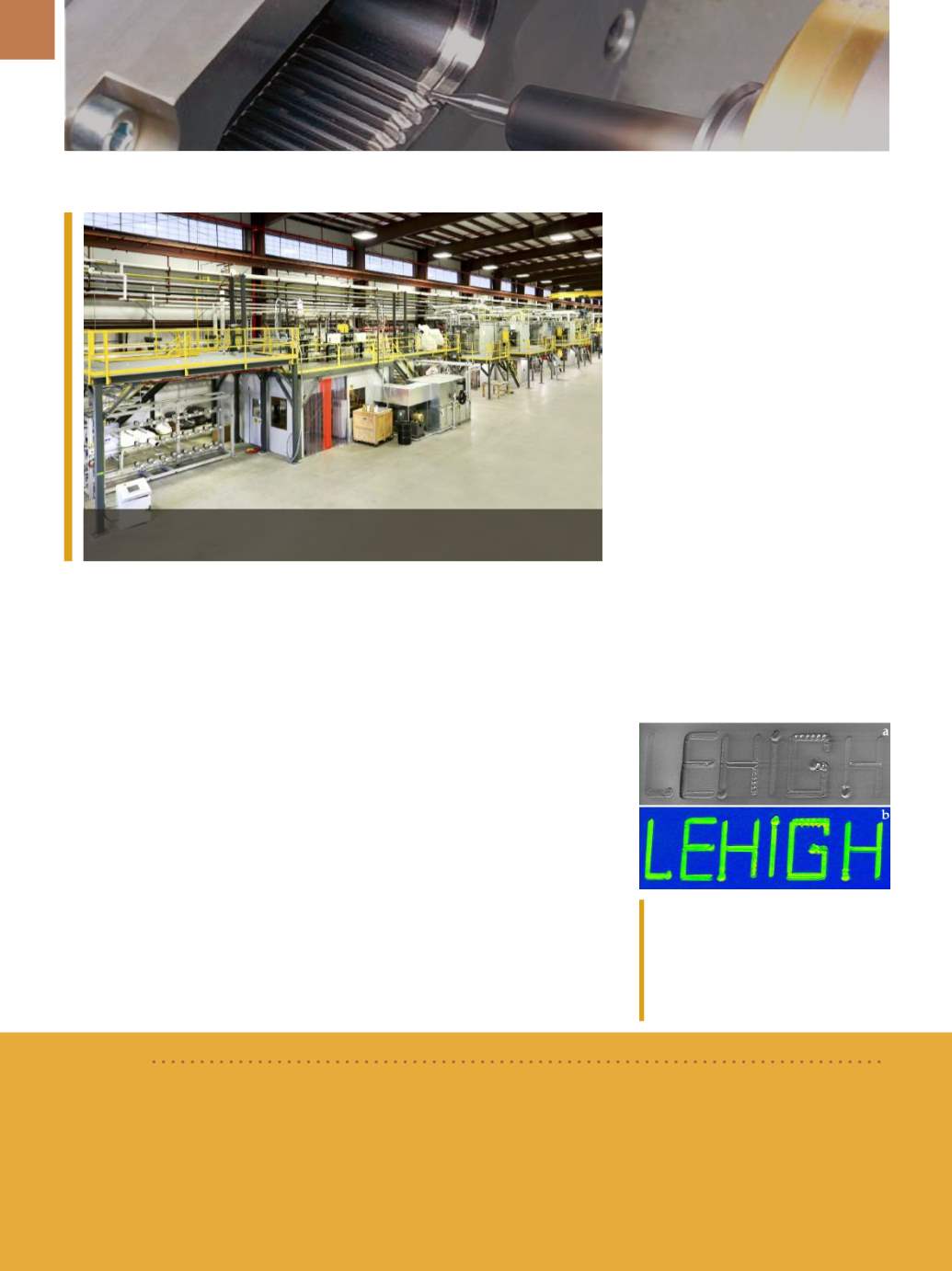
A D V A N C E D M A T E R I A L S & P R O C E S S E S | M A Y 2 0 1 6
1 6
PROCESS TECHNOLOGY
ORNL researchers demonstrated a production method that dramatically reduces the
cost and energy required to produce carbon fiber.
CARPET FIBER TO
CARBON FIBER
Researchers at the DOE’s Oak Ridge
National Laboratory (ORNL), Tenn.,
demonstrated a production method
for carbon fiber that uses the low cost,
acrylic fiber commonly found in car-
pets and clothing as a precursor mate-
rial. This process could reduce the cost
of carbon fiber by as much as 50% and
reduce the energy consumed in its pro-
duction by more than 60%.
To make carbon fiber, a car-
bon-containing polymer fiber precur-
sor—typically polyacrylonitrile (PAN)
that has been chemically optimized—is
subjected to an energy-intensive pro-
cess of controlled heating and stretch-
ing. It was suspected that textile-grade
PAN, which is chemically similar to
specialty PAN but costs roughly half
Scanning electron micrograph (a) and
image quality map (b) of the micrograph
demonstrate the ability to fabricate
patterned single-crystal architecture
on a glass surface. Courtesy of Dmytro
Savytskii.
BRIEFS
New websites were launched by
The Metal Powder Industries Federation
(MPIF),
APMI International,
and the
Center for Powder Metallurgy Technology
(CPMT), all in Princeton, N.J. The MPIF site includes a directory of powder
metallurgy (PM) fabricators and suppliers, a PM publications section hosted by Thomson Reuters Techstreet, and
educational video content. The APMI International site provides industry employment postings and information on
the Powder Metallurgy Technology Certification program, along with members-only access to an archive of the
Inter-
national Journal of Powder Metallurgy,
the
Who’s Who in Powder Metallurgy Membership Directory,
and a series of free
e-learning courses. On its website, CPMT offers information on current and completed technology programs, student
scholarships, and the CPMT/Axel Madsen Conference Grants program.
mpif.org,
mpif.org/apmi,
cpmtweb.org.
as much, could be used instead, but
laboratory-scale experiments weren’t
sufficient to demonstrate this. Using
ORNL’s Carbon Fiber Technology Facil-
ity, researchers were able to define a
production method that not only uses
the more affordable precursor, but also
is significantly more efficient. Because
more than 90% of the energy needed to
manufacture advanced composites is
consumed in manufacturing the carbon
fiber itself, the new method will enable
an earlier net energy payback. Mechan-
ical property analysis and automotive
industry prototyping are promising,
and ORNL is accepting license applica-
tions for the process.
ornl.gov.SINGLE-CRYSTAL SOLIDS
Scientists at Lehigh University,
Bethlehem, Pa., demonstrated a new
process to make solid materials in
single-crystal form, giving them the
properties required in high-tech applica-
tions such as lasers and semiconductors.
Because many solids decompose when
melted, the group devised a novel heat-
ing strategy to convert glass into a single
crystal without having it pass through a
gaseous or liquid phase. The research-
ers first use a laser to heat antimony-sul-
fide (Sb
2
S
3
) chalcogenide glass from the
ambient temperature to a crystalliza-
tion temperature well below its melting
point. Next, they use electron diffraction
andmicroscopy color mapping to detect
the orientation of atomic configurations
and prove single crystallinity at different
places on the sample. “Once we make
the single-crystal line, we backtrack to
get additional parallel single-crystal
lines and eventually a single-crystal-
layer surface on top of the glass. We can
stitch these lines to convert the entire
glass surface into a single crystal,” says
Himanshu Jain, professor of materials
science and engineering.
lehigh.edu.