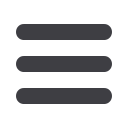
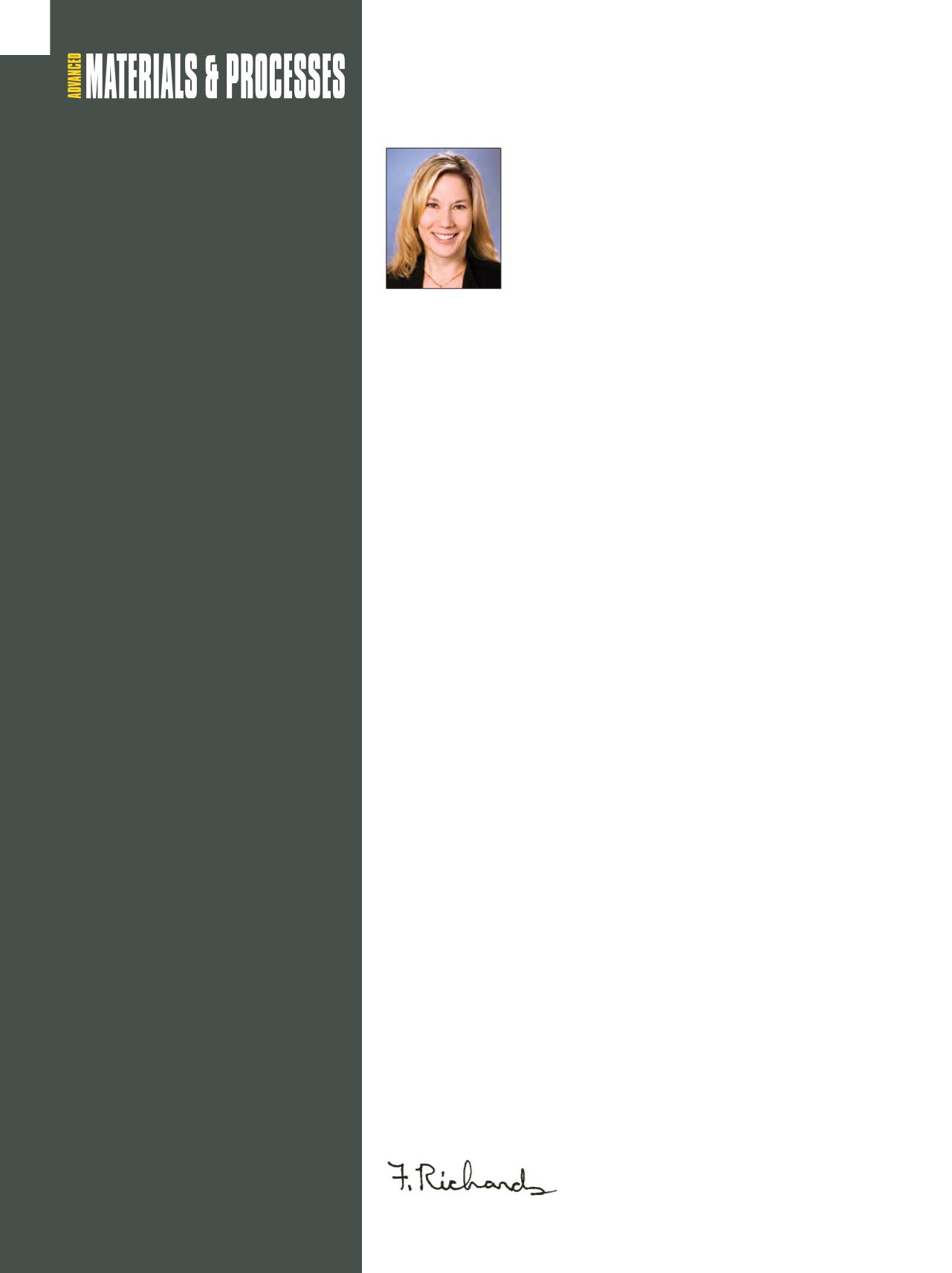
4
A D V A N C E D M A T E R I A L S & P R O C E S S E S | M A Y 2 0 1 5
ASM International
9639 Kinsman Road, Materials Park, OH 44073
Tel: 440.338.5151 • Fax: 440.338.4634
Frances Richards,
Editor-in-Chief
frances.richards@asminternational.orgJulie Lucko,
Editor
julie.lucko@asminternational.orgJim Pallotta,
Creative Director
jim.pallotta@asminternational.orgKate Fornadel,
Layout and Design
kate.fornadel@asminternational.orgAnnie Beck,
Production Manager
annie.beck@asminternational.orgPress Release Editor
magazines@asminternational.orgEDITORIAL COMMITTEE
Yu-Ping Yang,
Chair,
EWI
Jaimie Tiley,
Vice Chair,
U.S. Air Force
Research Lab
Mario Epler,
Past Chair,
Carpenter
Technology Corp.
Craig Clauser,
Board Liaison
Kathryn Dannemann,
Board Liaison
Laura Addessio,
PCC Structurals Inc.
Arvind Agarwal,
Florida International
University
Gerald Bruck,
Siemens Westinghouse
Power Corp.
Steven Claves,
Alcoa Inc.
Adam Farrow,
Los Alamos National Lab
Nia Harrison,
Ford Motor Co.
Alan Luo,
The Ohio State University
Roger Narayan,
UNC-NCSU
Somuri Prasad,
Sandia National Lab
Fei Ren,
Temple University
Kumar Sridharan,
University of Wisconsin
ASMBOARDOF TRUSTEES
Sunniva R. Collins,
President
Jon D. Tirpak,
Vice President
Craig D. Clauser,
Treasurer
C. Ravi Ravindran,
Immediate Past President
Iver Anderson
Kathryn Dannemann
Mitchell Dorfman
James C. Foley
Jacqueline M. Earle
John R. Keough
Zi-Kui Liu
Tirumalai S. Sudarshan
David B. Williams
Terry F. Mosier,
Secretary and
InterimManaging Director
STUDENT BOARDMEMBERS
Virginia K. Judge, Anthony Lombardi,
Myrissa N. Maxfield
Individual readers of Advanced Materials & Processes may,
without charge, make single copies of pages therefrom for per-
sonal or archival use, or may freely make such copies in such
numbers as are deemed useful for educational or research
purposes and are not for sale or resale. Permission is granted
to cite or quote fromarticles herein, provided customary
acknowledgment of the authors and source is made.
M
any fascinating developments are taking place in the
aeronautics industry, andwe hope you enjoy our an-
nual aerospace issue. Compositematerials that offer
high strength and low weight are one promising area. Just
recently, NASA created a special partnership, the Advanced
Composites Consortium, to develop composite materials
for future aircraft designs. The public-private partnership
includes the Federal Aviation Administration (FAA), General
Electric Aviation (GE), Lockheed Martin Aeronautics Co., Boeing Research & Tech-
nology, a team fromUnited Technologies Corp. led by Pratt & Whitney, and the Na-
tional Institute of Aerospace, who will manage administrative functions.
NASA formed the consortium in support of the Advanced Composites
Project, part of the Advanced Air Vehicles Program in the agency’s Aeronautics
Research Mission Directorate. The goal is to reduce product development and
certification timelines by 30% for composites used in aeronautics applications.
If you’re attending AeroMat this month in Long Beach, Calif., be sure to check
out the composites sessions, which cover a range of topics from fundamental
science and technology to process development and fabrication.
Another important area—also featured in several AeroMat sessions—cov-
ers high temperature and turbine materials. Advances in alloys, ceramics, inter-
metallics, and coatings will be presented, emphasizing how integrated compu-
tational materials engineering enables cost-effective, rapid development. Along
these lines, be sure to read Mike Nathal’s article, in which he makes the case for
what appears to be “low-hanging fruit” to replace single crystals as high-pres-
sure turbine blades—oxide dispersion strengthened (ODS) Ni-base alloys (p. 21).
Arguably, the hottest topic in aerospace parts production these days is the
vast promise of 3D printing, due to its ability to create intricate components
in significantly less time than traditional methods such as casting. Just a few
weeks ago, the FAA cleared the first 3D-printed part to fly in a commercial jet
engine from GE: It’s a fist-sized piece of silver metal, which houses the compres-
sor inlet temperature sensor inside a jet engine. GE Aviation is now working
with Boeing to retrofit more than 400 GE90-94B jet engines with the 3D-printed
part. In addition, GE also began flight tests with the next-generation LEAP jet
engine, which holds 19 3D-printed fuel nozzles. The engine, which will power
new narrow-body planes like the Boeing 737MAX and the Airbus A320neo, was
developed by CFM International, a 50/50 joint venture between GE Aviation and
France’s Safran (Snecma).
It would normally take GE several years to design and prototype a part like
the sensor housing, but the team was able to shave as much as a year from the
process. “The 3D printer allowed us to rapidly prototype the part, find the best
design, and move it quickly to production,” says Bill Millhaem, general manager
for the GE90 and GE9X engine programs. “We could never do this using the tra-
ditional casting process, which is how the housing is typically made.”
Andnowfor that shot of espresso. TheSpaceXDragoncargocapsulehooked
up with the International Space Station in mid-April, delivering groceries, sup-
plies, and an espresso machine. Italy’s space agency made it happen: The new
machine is the result of collaborations between engineers from the country’s
aerospace industry and the Lavazza coffee company. It’s the little things in life
that mean the most, and happy astronauts are likely more productive.
frances.richards@asminternational.orgAEROSPACE TODAY: COMPOSITES,
3D PRINTING, &A SHOT OF ESPRESSO