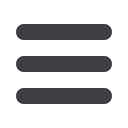
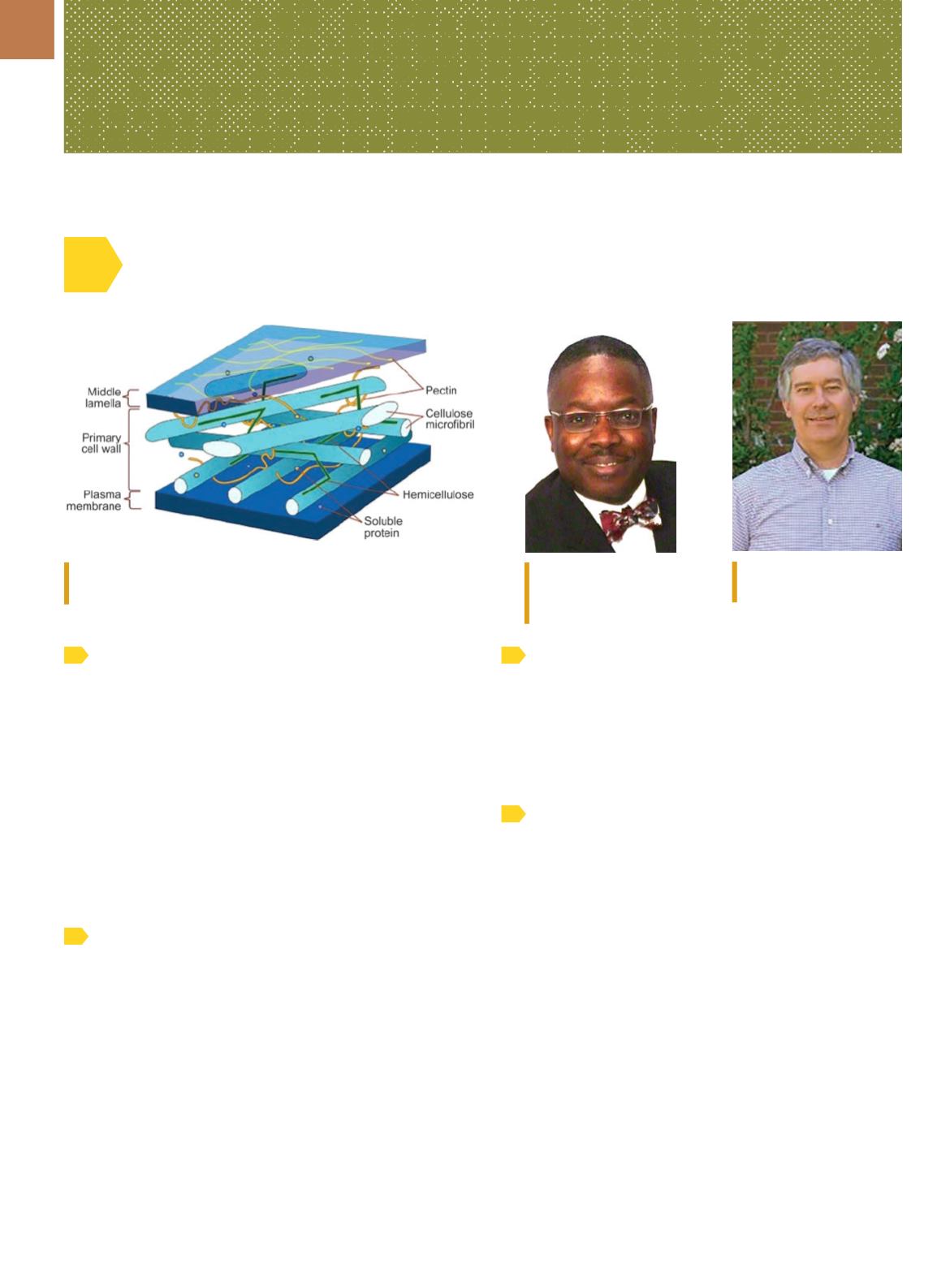
A D V A N C E D M A T E R I A L S & P R O C E S S E S | M A R C H 2 0 1 5
5 8
SUCCESS ANALYSIS
SPECIMEN: EARTH-FRIENDLY COMPOSITES
VITAL STATISTICS
A new technology aims to use natural wood fibers to rein-
force plastic materials. If successful, researchers believe it could
revolutionize the composites industry, especially manufactur-
ing sectors that rely on these materials, such as automotive and
aerospace. Currently, the composites industry combines wood
particles
—rather than
fibers
—with its polymers. “This saves
money, but is a less optimum way of doing it,” says Joshua
Otaigbe, a professor in The University of Southern Mississippi’s
School of Polymers andHigh PerformanceMaterials. “We are ex-
tracting fibers, which are different from particles. The fiber is a
lot stiffer and stronger than thewood particles, and provides the
reinforcing capability for the plastic.”
SUCCESS FACTORS
Using wood fibers instead of particles in the direct conver-
sion of polymer building blocks called monomers also allows
manufacturers to eliminate the melting stage, when materials
are shaped and later solidified into various products. “With fi-
bers in the polymer matrix, we can shape it without having to
melt it,” says Otaigbe.
The process under development involves taking the
wood fibers, usually within paper, placing them in a mold, and
then injecting a reaction mixture used to make the polymers.
Scientists then raise the temperature to 150°C, relatively low
compared to traditional melting methods. “The mixture forms
a composite in a matter of minutes,” explains Otaigbe. Lower
temperatures are important because wood fibers tend to de-
grade at temperatures above 190°C.
ABOUT THE INNOVATORS
The National Science Foundation is funding the work
through its structural materials and mechanics program of the
division of civil, mechanical, and manufacturing innovation.
Otaigbe is collaborating with John Nairn, the Richardson Chair
in wood science and engineering at Oregon State University.
The two researchers are sharing the grant.
WHAT’S NEXT
Otaigbe is also studying ways to generate nanostruc-
tured hybrid glass/organic polymer materials via molecular
level mixing of the components in a liquid state, creating nov-
el hybrids impossible to produce using conventional meth-
ods. These products could translate into improved energy
efficiency for such applications as high-powered laser fusion
systems, biomaterials, storage materials for nuclear wastes,
and as a component in load-bearing organic-inorganic hybrid
composites.
Contact Details
Joshua Otaigbe
The University of Southern Mississippi
118 College Dr., #5050
Hattiesburg, MS 39406
601.266.5596
joshua.otaigbe@usm.edu www.usm.eduSchematic of a wood cell wall, showing the substructure of
load-bearing cellulose microfibrils. Courtesy of U.S. Forest Service.
Joshua Otaigbe, The
University of Southern
Mississippi.
John Nairn, Oregon State
University