
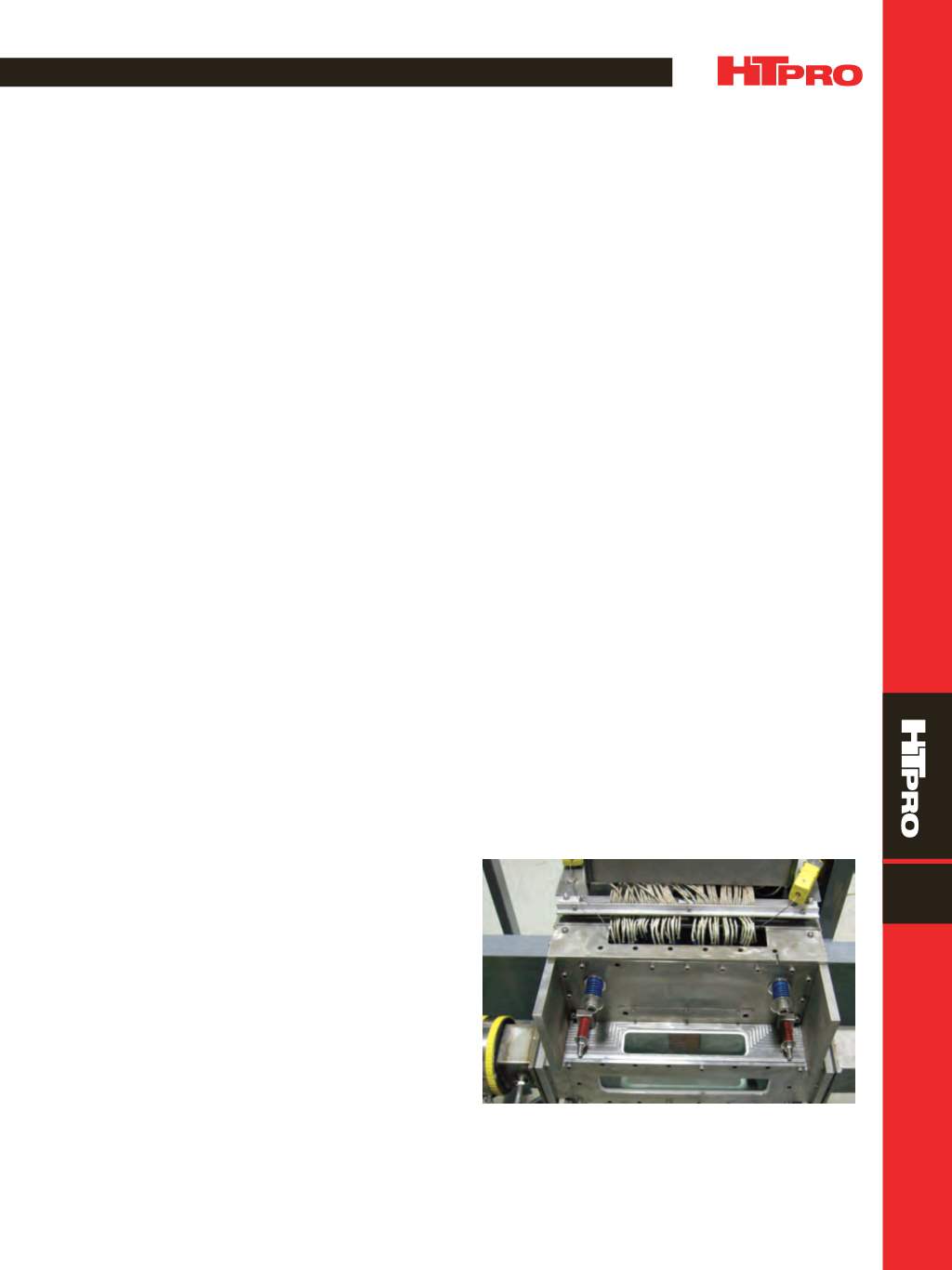
A D V A N C E D
M A T E R I A L S
&
P R O C E S S E S | F E B R U A R Y / M A R C H
2 0 1 7
6 3
FEATURE
13
C
omputational analysis, a tool that has helped opti-
mize many heat treating processes, has yet to have
an extensive impact on liquid quenching. Quench-
ing in a vaporizable liquid is a critical production step for
many metal parts, but the complexity of the physics make
it a difficult process to simulate. Rigorous physics-based
boiling models can yield good results, but are impractical
for cases of industrial interest. An alternative, data-driven
approach presented here holds promise, however, and is
scoring well when tested under realistic conditions.
A MODELING DILEMMA
Heat treat processes incorporating a liquid or gas
quenching step are essential to the quality of manufac-
tured metal components. The rapid cooling that occurs
during quenching largely determines phase distribu-
tion, microstructure, residual stress, and distortion in the
as-quenched part. Manufacturers, naturally, would like
to better control these pivotal material properties, and
are looking to numerical analysis tools for the necessary
leverage.
Numerical methods and tools have been used to gain
a better understanding of many heat treating operations,
leading to significant process improvements. But their
use in the area of liquid quenching has been much less
extensive. Simulating the process of quenching has been
a persistent challenge because of the difficulty in predict-
ing surface heat flux rates due to boiling of the vaporizable
quenchant.
Materials scientists confronting this issue will often
conduct instrumented tests on the part in question, then
use “inverse analyses” to extract surface heat flux values
from the measured internal temperatures. This approach
is time consuming, expensive, and subject to non-unique
solutions. Further, the resulting heat flux values are only
applicable to the specific part and quenching environ-
ment. If a change will be made in processing conditions,
the experiment must be repeated.
A purely computational approach—one that predicts
the explosive formation of vapor and release of bubbles
based on the underlying physics—is theoretically possible,
but it would be impractical in applications of industrial
interest because length scales and time frames differ by
orders of magnitude across the working domains.
An alternative approach, and the focus of this article,
incorporates both experimental and computational meth-
ods, benefiting from the combination of strengths. Elusive
surface heat flux rates are determined experimentally in
a precisely controlled flow boiling test system. This data
is then used to build computational fluid dynamics (CFD)
models that are proving to be quite accurate in quenching
process simulations.
FLOW BOILING DATA COLLECTION
As part of an Air Force Research Laboratory sponsored
SBIR study, a group of investigators developed an experi-
mental facility to collect flow boiling heat flux data for vapor-
izable quenchants. In the heart of the system, as shown in
Fig. 1, a test coupon embedded in the wall of a flow channel
is exposed to quenchant circulating at controlled speeds.
The heat source, a bank of cartridge heaters with an output
ACCURATE MODELING OF QUENCHING PROCESSES USING
CFD AND A FLOW BOILING DATABASE
Experimentally derived surface heat flux rate data and CFD software are helping researchers more
accurately simulate liquid quenching processes.
Andrew L. Banka* and Jeffrey D. Franklin,*
Airflow Sciences Corp., Livonia, Mich.
Fig. 1 —
Flow channel for measuring flow boiling surface heat flux
rates.
*Member of ASM International