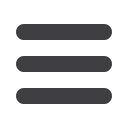
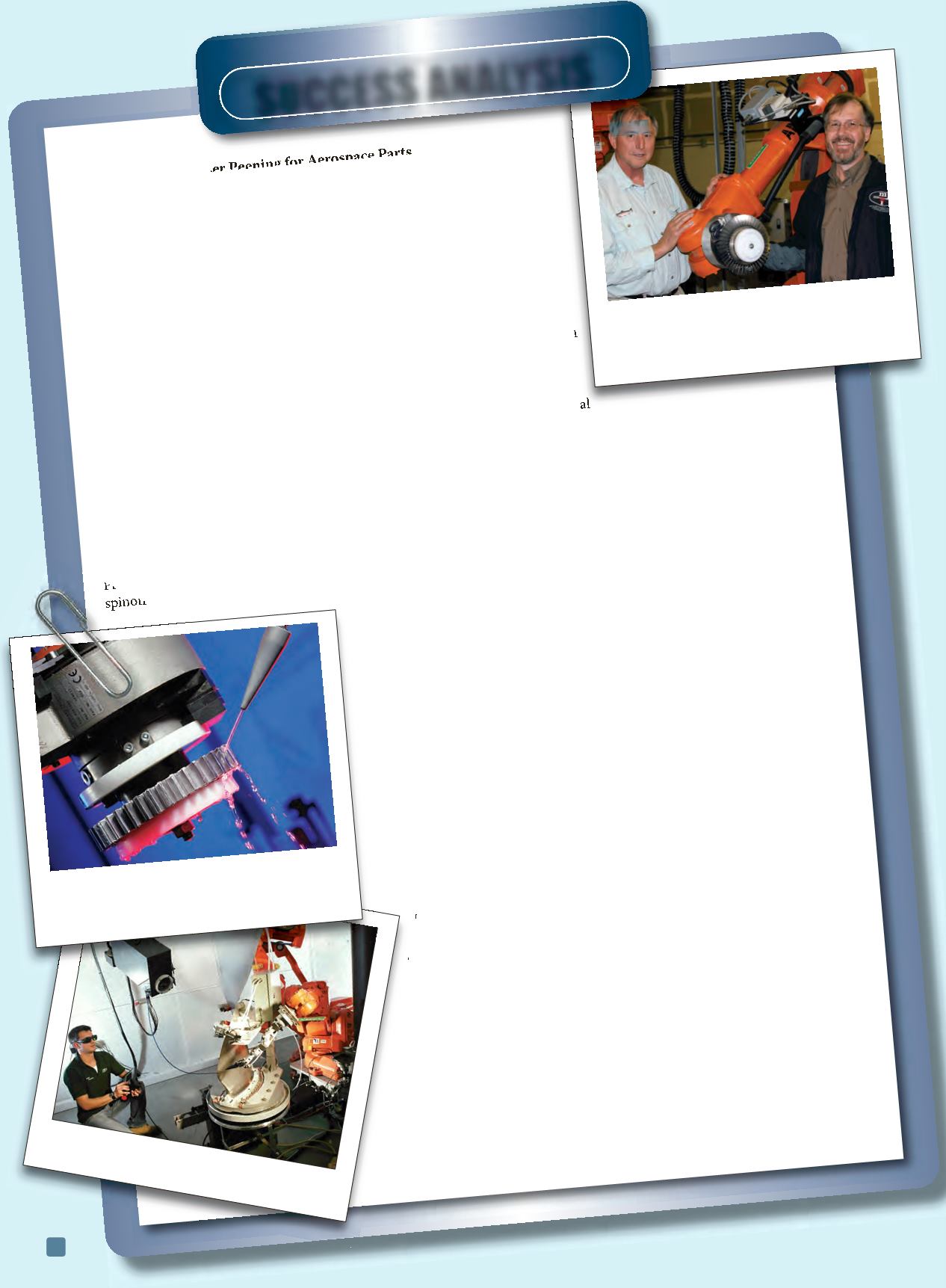
68
Specimen Name:
Laser Peening for Aerospace Parts
Vital Statistics:
One method widely used to strengthen metal is peening, which involves
bombarding it with tiny metal balls known as shot to induce a layer of compressive
stress at the surface to prevent fatigue and reduce corrosion. Taking it up a notch
from traditional shot peening is laser peening, a process that induces deep
compressive stress to significantly extend the service life of components.
Laser peening, invented in the 1970s, uses short bursts of intense laser light
to create pressure pulses on metal surfaces, which generate shock waves that
travel into the metal and compress it. In the early days, the technology was not
suitable for commercial parts due to high costs and slow lasers. Now, one version
of modern laser peening employs a unique, high-energy laser developed at
Lawrence Livermore National Laboratory (LLNL) fired at the surface of a metal
part to generate pressure pulses of one million psi. These pulses propagate
through the part to plastically compress the metal and generate an area of residual
compressive stress. Peening helps components last longer and resist cracking. Applications include aerospace engine
blades and wings, as well as turbine blades used in gas and nuclear reactors for power generation.
Success Factors:
Lloyd Hackel and Brent Dane—former LLNL researchers with nearly 40 years of combined experience—began
developing commercial laser peening technology while working on a project funded by DARPA (Defense Advanced
Research Projects Agency) and the U.S. Navy and Air Force. Their project, within LLNL’s Science and Technology
Program, aimed to develop laser technology for x-ray lithography and satellite imaging research. This technology, a
spinoff from the DOE’s Inertial Confinement Program, was eventually used to develop laser peening for commercial use.
Hackel and Dane’s research caught the eye of Metal Improvement Co.
(MIC), Paramus, N.J., a business unit of Curtiss-Wright that performs both
traditional shot peening and now laser peening for the majority of aircraft
engine and airframe builders around the world. MIC executives wondered if
the men could use their expertise to develop disruptive laser peening
technology for manufacturing purposes. Hackel and Dane set out to develop a
neodymium-doped glass laser that produces one billion watts of peak power in
20-billionth-of-a-second pulses—roughly the same output as a large
commercial power plant. In 1997, LLNL’s Industrial Partnerships Office
worked with the researchers and MIC to develop a formal agreement to
commercialize the technology.
About the Innovators:
In 2003, Hackel and Dane left the Lab for MIC because they saw industry as
an opportunity to push their technology further. Working out of an MIC
regional R&D center in Livermore, the men expanded their laser peening
technology, enabling MIC to win large contracts to peen more than 40,000 jet
engine fan blades and 1000 discs. MIC’s laser peening work is estimated to
have saved the aviation industry hundreds of millions of dollars in parts
and service due to longer lasting components.
What’s Next:
Potential applications include preventing metal erosion and corrosion
on ship propellers, rudders, and thrusters, and fortifying metals used in
high-performance automotive engines, deep-water oil drilling rigs, welds in
nuclear power plants and for nuclear waste storage containers, and medical
devices such as hip implants.
Contact Details:
C. Brent Dane, Director of Laser Technology
Curtiss-Wright Surface Technologies
Metal Improvement Comp
any7655 L
ongard Rd., Livermore, C A 94551925/960-1090,
cbrent.dane@cwst.com, www.cwst.com
An MIC engineer checks the placement of
laser spots prior to fully automated
processing.
As an invisible laser beam peens the roots
of gear teeth, a robotically positioned
nozzle delivers a flow of water that tamps
the plasma.
Former LLNL researchers Lloyd Hackel (left)
and Brent Dane with a robot used to laser
peen parts for aviation and other industries
at MIC’s Livermore R&D Center. Courtesy of
Julie Russell/LLNL.
SucceSS AnAlySiS
ADVANCED MATERIALS & PROCESSES •
MAY 2014